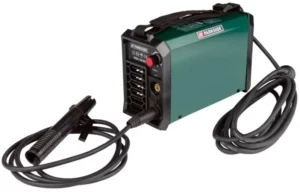
PISG 120 B3 Inverter Welder Instruction
Manual
INVERTER WELDER
Operation and Safety Notes Translation of the original instructions
Before reading, unfold the page containing the illustrations and familiarise yourself with all functions of the device.
List of pictograms used
![]() |
Caution! Read the operating instructions! | ![]() |
Risk of serious injury or death. |
![]() |
Power input; Number of phases and Alternating current symbol and rated value of the frequency. |
![]() |
Caution! Risk of electric shock! |
![]() |
Important note! | ||
![]() |
Do not dispose of electrical devices in household waste! | ![]() |
Dispose of the device and packaging in an environmentally friendly manner. |
![]() |
Never use the device in the open or when it’s raining! | ![]() |
Manual arc welding with encased rod electrodes. |
![]() |
Electric shock from the welding electrode can be fatal! | ![]() |
Protection class. |
![]() |
Inhalation of welding fumes can endanger your health. | ![]() |
Suitable for welding under increased electrical hazards. |
![]() |
Welding sparks can cause an explosion or fire. | ![]() |
Single-phase static frequency converter-transformer- commutator. |
![]() |
Arc beams can damage your eyes and injure your skin. | H | Insulation class. |
![]() |
Electromagnetic fields can disrupt the function of cardiac pacemakers. | ![]() |
Direct current. |
![]() |
Warning: Potential hazards! | ![]() |
Made from recycling material. |
X % | Duty cycle. | U0 | Rated value of the open-circuit voltage |
I1 max | Greatest rated value of the mains current | U1 | Rated value of the mains voltage |
I2 max | Greatest rated value of the welding current | U2 | Standardized operating voltage |
I1 eff | The effective value of the greatest mains current |
INVERTER WELDER PISA 120 B3
Introduction
Congratulations!
You have purchased one of our high-quality products. Please familiarise yourself with the product before using it for the first time. Please also read the safety instructions carefully. This product must be set up or used only by people who have been trained to do so.
KEEP OUT OF THE REACH OF CHILDREN!
Intended use
This welding device is ideal for welding metals such as carbon steel, steel alloy, other stainless steel, copper, aluminium, titanium, etc. The product has a control lamp, a heat protection display, and a cooling fan. In addition, it is fitted with a carrying strap so that the product can be lifted and moved safely. If it is not handled properly the product can be dangerous for individuals, animals, and property. Use the product only as described and only for the specific applications as stated. Keep these instructions in a safe place. Ensure you hand over all documentation when passing the product on to anyone else. Any use that differs from the intended use as stated above is prohibited and potentially dangerous. Damage or injury caused by misuse or disregarding the above warning is not covered by the warranty or any liability on the part of the manufacturer. The device is intended for professional use. Commercial use will void the guarantee.
Package contents
1 | Inverter welder |
1 | Welding mask |
2 | Welding cables |
1 | Combi wire brush with slag hammer |
1 | Carrying strap |
5 | Welding electrodes (2 x 1.6 mm; 2 x 2.0 mm; 1 x 2.5 mm) |
1 | Operating instructions |
Parts description
1. Carrying strap | 7. Welding mask |
2. Rotary knob | 8. Handle |
3. Control lamp for overheating | 9. ON/OFF switch |
4. Ground terminal | 10. Power cable 4 m |
5. Electrode holder | 11. Protective glass |
6. Combi wire brush with slag hammer | 12. Welding electrodes |
Technical specifications
Mains connection: | 230 V 50/60 Hz |
Nominal power input: | 3.6 kW |
Max. welding current and the appropriate standardized operating voltage: | 10 A/20.4 V – 120 A/24.8 V |
Rated value of the mains voltage: | U1:230 V |
Greatest rated value of the mains current: | I1max: 22 A |
Maximum effective input current: | I1eff: 11 A |
Rated value of the open-circuit voltage: | U0: 80 V |
Protection class: | IP21S |
Weight: | approx. 3 kg |
Duty cycle X: | 30% at 40 °C and 120 A |
Falling characteristic | |
Material thicknesses which can be welded: | 1.5 mm —3.0 mm |

Please read the operating instructions with care and observe the notes described. Familiarise yourself with the device, its proper use, and the safety instructions based on these operating instructions. The rating plate contains all technical data of this welding device; please learn about the technical features of this device.
Keep the packaging material away from small children. There is a risk of suffocation!
- This device may be used by children aged 16 years and older, and by persons with reduced physical, sensory or mental capacities, or a lack of experience and knowledge if they are supervised or have been instructed in how to use the device safely and understand the dangers that may arise when using it. Do not allow children to play with the device. Cleaning and day-to-day maintenance must not be performed by children without supervision.
- Repairs or/and maintenance work must only be carried out by qualified electricians.
- Only use the weld cable provided in the scope of delivery.
- During operation, the device should not be positioned directly on the wall, covered, or jammed between other devices so that sufficient air can be absorbed through the ventilation slots. Make sure that the device is correctly connected to the supply voltage. Avoid any form of tensile stress of the power cable. Disconnect the plug from the socket prior to setting up the device in another location.
- If the device is not in operation, always switch it off by pressing the ON/OFF switch. Place the electrode holder on an insulated surface and only remove it from the holder after allowing it to cool down for 15 minutes.
- Pay attention to the condition of the welding cable, electrode holder, and earth terminal. The wear and tear of the insulation and the live parts can lead to hazards and reduce the quality of the welding work.
- Arc welding creates sparks, molten metal parts, and smoke. Therefore ensure that: All flammable substances and/or materials are removed from the work station and its immediate surrounding.
- Ensure the workstation is ventilated.
- Do not weld on containers, vessels, or tubes that contain or contained flammable liquids or gases.
Avoid any form of direct contact with the welding current circuit. The open-circuit voltage between the electrode holder and earth terminal can be dangerous, there is a risk of electric shock.
- Do not store or use the device in a damp or wet environment or in the rain. Protection rating IP21S is applicable in this case.
- Protect your eyes using the appropriate protective glasses (DIN level 9-10), which are fastened to the supplied welding Safety instructions mask. Wear gloves and dry protective clothing that are free of oil and grease to protect the skin from exposure to ultraviolet radiation of the arc.
Do not use the welding power source to defrost pipes.
Please note:
- The light radiation emitted by the electric arc can damage the eyes and cause burns to the skin.
- Arc welding creates sparks and drops of melted metal. The welded workpiece starts to glow and remains hot for a relatively long period. Therefore, do not touch the workpiece with bare hands.
- Arc welding can cause vapours to be released that may be hazardous to health. Be careful not to inhale these vapours.
- Protect yourself from the harmful effects of the electric arc and keep people that are not involved in the work away from the arc maintaining a distance of at least 2 m.
ATTENTION!
- During the operation of the welding device, other consumers may experience problems with the voltage supply depending on the network conditions at the connection point. In case of doubt, please contact your energy supply company.
- During the operation of the welding device, other devices may malfunction, e.g. hearing aids, cardiac pacemakers, etc.
- Potential hazards during electric arc welding
There are a series of potential hazards that can occur during electric arc welding. It is therefore particularly important for the welder to observe the following rules to avoid endangering him/ herself and others and to prevent damage to people and the device.
- Work on the voltage side, e.g.on cables, plugs, sockets etc., may only be carried out by qualified electricians according to national and local regulations.
- In the event of accidents, disconnect the welding device from the mains voltage immediately.
- If electrical contact voltages occur, switch off the device immediately and have it checked by a qualified electrician.
- Always ensure good electrical contacts on the welding current side.
- Always wear insulating gloves on both hands during welding work. These provide protection from electrical shocks (no-load voltage of the welding current circuit), harmful radiations (heat and UV radiation) and incandescent metal and splashes of slag.
- Wear sturdy, insulating shoes. The shoes should also insulate when exposed to moisture. Loafers are not suitable as falling incandescent metal droplets can cause burns.
- Wear suitable protective clothing, no synthetic garments.
- Do not look into the electric arc without eye protection; only use a welding mask with the prescribed protective glass as per DIN. In addition to light
and heat radiation, which can dazzle or cause burns, the electric arc also emits UV radiation. Without suitable protection, the invisible ultraviolet radiation can cause very painful conjunctivitis which is not apparent until several hours later. Furthermore, UV radiation can cause burns with sunburn-like effects on unprotected parts of the body. - Any persons in the vicinity of the electric arc or helpers must also be informed of the dangers and be equipped with the necessary protective equipment. If necessary, set up protective walls.
- Ensure an adequate supply of fresh air whilst welding, particularly in small spaces, as it produces smoke and harmful gases.
- No welding work may be carried out on containers that have been used for storing gases, fuels, mineral oils or similar – even if they have been empty for a long time – as possible residues may present a risk of explosion.
- Special regulations apply in rooms where there is a risk of fire or explosion.
- Welded joints that are subject to heavy stress loads and are required to comply with certain safety requirements may only be carried out by specially trained and certified welders. Examples of this are pressure vessels, running rails, tow bars, etc.
ATTENTION! Always connect the earth terminal as close as possible to the point of weld to provide the shortest possible path for the welding current from the electrode to the earth terminal. Never connect the earth terminal to the housing of the welding device! Never connect the earth terminal to earthed arts far away from the workpiece, e.g. a water pipe in another corner of the room. This could otherwise damage the protective bonding system of
the room you are welding.
- Do not use the welding device in the rain.
- Do not use the welding device in a moist environment.
- Only place the welding device on a level surface.
- The output is rated at an ambient temperature of 20 °C. The welding time can be reduced at higher temperatures.
Risk of electric shock:
Electric shock from the welding electrode can be fatal. Do not weld in rain or snow. Wear dry insulating gloves. Do not touch the electrodes with bare hands. Do not wear wet or damaged gloves. Protect yourself from electric shock with insulation against the workpiece. Do not open the device housing.
Danger from welding fumes:
- Inhalation of welding fumes can endanger health. Do not keep your head in the fumes. Use the equipment in open areas. Use extractors to remove the fumes.
Danger from welding sparks:
- Welding sparks can cause an explosion or fire. Keep flammable substances away from the welding location. Do not weld next to flammable substances. Welding sparks can cause fires. Keep a fire extinguisher close by and an observer should be present to be able to use it immediately. Do not weld on drums or any other closed containers.
Danger from arc beams:
- Arc beams can damage your eyes and injure your skin.
Wear a hat and safety goggles.
Wear hearing protection and high, closed shirt collars.
Wear welding safety helmets and make sure you use the appropriate filter settings. Wear complete body protection.
Danger from electromagnetic fields:
- Welding current generates electromagnetic fields. Do not use if you have a medical implant. Never wrap the welding cable around your body. Guide welding cables together.
Welding mask-specific safety instructions
- With the help of a bright light source (e.g. lighter) examine the proper functioning of the welding mask prior to starting with any welding work.
- Weld spatters can damage the protective screen. Immediately replace damaged or scratched protective screens.
- Immediately replace damaged or highly contaminated or splattered components.
- The device must only be operated by people over the age of 16.
- Please familiarise yourself with the welding safety instructions. Also, refer to the safety instructions of your welding device.
- Always wear a welding mask while welding. If it is not used, you could sustain severe lesions to the retina.
- Always wear protective clothing during welding operations.
- Never use the welding mask without the protective screen.
- Regularly replace the protective screen to ensure good visibility and fatigue-proof work.
An environment with increased electrical hazard
When welding in environments with increased electrical hazards, the following safety instructions must be observed. Environments with increased electrical hazard may be encountered, for example:
- In workplaces where the space for movement is restricted, such that the welder is working in a forced posture (e.g.: kneeling, sitting, lying) and is touching electrically conductive parts;
- In workplaces which are restricted completely or in part in terms of electrical conductivity and where there is a high risk through avoidable or accidental touching by the welder;
- In wet, humid, or hot workplaces where the air humidity or weld significantly reduces the resistance of human skin and the insulating properties or effect of protective equipment.
Even a metal conductor or scaffolding can create an environment with increased electrical hazards.
In this type of environment, insulated mats and pads must be used. Furthermore, gauntlet gloves and head protection made of leather or other insulating materials must be worn to insulate the body against Earth. The welding power source must be located outside the working area or electrically conductive surfaces and out of the welder’s reach.
Additional protection against a shock from the mains’ power in the event a fault can be provided by using a fault-circuit interrupter, which is operated with a leakage current of no more than 30 mA and covers all mains-powered devices in close proximity. The fault-circuit interrupter must be suitable for all types of current.
There must be means of rapid electrical isolation of the welding power source or the welding circuit (e.g. emergency stop device) which are easily accessible.
When using welding devices under electrically dangerous conditions, the output voltage of the welding device must be greater than 113 volts when idling (peak value). Based on the output voltage this welding device may be used in these conditions.
Welding in tight spaces
When welding in tight spaces this may pose a hazard through toxic gases (risk of suffocation). In tight spaces, you may only weld if there are trained individuals in the immediate vicinity who can intervene if necessary. In this case, before starting the welding procedure, an expert must carry out an assessment in order to determine what steps are necessary, in order to guarantee safety at work and which precautionary measures should be taken during the actual welding procedure.
Total of open-circuit voltages
When more than one welding power source is operated at the same time, their open-circuit voltages may add up and lead to an increased electrical hazard. Welding power sources must be connected in such a way that the danger is minimized. The individual welding power sources, with their individual control units and connections must be clearly marked, in order to be able to identify which device belongs to which welding power circuit.
Using shoulder straps
Welding must not take place if the welding power source is being carried e.g. with a shoulder strap. This is intended to prevent:
- The risk of losing your balance if the lines or hoses which are connected are pulled
- The increased risk of an electric shock as the welder comes into contact with the earth if he/she is using a Class I welding power source, the housing of which is earthed through its conductor.
Protective clothing
At work, the welder must protect his/her whole body by using appropriate clothing and face protection against radiation and burns. The following steps must be observed:
- Wear protective clothing prior to welding work
- Wear gloves.
- Open windows or use fans to guarantee air supply.
- Wear safety goggles and a face mask.
- Gauntlet gloves made of a suitable material (leather) must be worn on both hands. They must be in perfect condition.
- A suitable apron must be worn to protect clothing from flying sparks and burns. When specific work, e.g. overhead welding, is required, a protective suit must be worn and, if necessary, even head protection.
- Gauntlet gloves made of a suitable material (leather) must be worn on both hands. They must be in perfect condition.
- A suitable apron must be worn to protect clothing from flying sparks and burns. When specific work, e.g. overhead welding, is required, a protective suit must be worn and, if necessary, even head protection.
Protection against rays and burns
- Warn of the danger to the eyes by hanging up a sign saying “Caution! Do not look into flames!”. The workplaces must be shielded so that the persons in the vicinity are protected. Unauthorised persons must be kept away from welding work.
- The walls in the immediate vicinity of fixed workplaces should neither be bright coloured or shiny. Windows up to head height must be protected to prevent rays from penetrating or reflecting through them, e.g. by using suitable paint.
EMC Device Classification
According to the standard IEC 60974-10, this is a welding device in electromagnetic compatibility Class A. Class A devices are devices that are suitable for use in all other areas except living areas and areas that are directly connected to a low-voltage supply main that (also) supplies residential buildings. Class A devices must adhere to the Class A limit values.
WARNING NOTICE: Class A devices are intended for use in an industrial environment. Due to the power-related as well as the radiated interference variables, difficulties might arise in ensuring electromagnetic compatibility in other environments.
Even if the device complies with the emission limit values in accordance with the standard, such devices can still cause electromagnetic interference insensitive systems and devices. The user is responsible for faults caused by the arc while working, and the user must take suitable protective measures. In doing so, the operator must consider the following:
- network, control, signal and telecommunication lines
- computers and other microprocessor-controlled devices
- TVs, radios and other playback devices
- electronic and electrical safety equipment
- people with cardiac pacemakers or hearing aids
- measurement and calibration devices
- interference immunity of other equipment nearby
- the time of day at which the work is being done. The following is recommended to reduce possible interference radiation:
- equip the mains connection with a mains filter
- service the device regularly and keep it in good condition
- welding cables should be completely uncoiled and run as close to parallel with the floor as possible
- if possible, devices and systems at risk from interference radiation should be removed from the work area or shielded.
The product is intended solely for professional use.
Before use
Take the device and accessories out of the packaging and check them for damage (e.g. transport damage).
- Fix the carrying strap 1 onto the device (see Fig. C1 – C4).
Fit welding mask
- Fit the handle 8 onto the welding mask 7, as shown in Fig. A.
- Fit the protective glass 11 onto the welding mask 7, as shown in Fig. A.
- The protective glass 11 must be pushed in from the top.
Note: If you are not able to push the protective glass 11 in fully, gently press on the outside of the protective glass 11
Using the device
Note: The welding device is designed for welding with electrodes.
- Use the electrode holder clamps without protruding bracket screws, which meet the current safety standards.
- Make sure that the ON/OFF switch 9 is set to position “O” (“OFF”) or that the power cable 10 is not plugged into the socket.
- Connect the welding cable according to its polarity and in accordance with the specifications of the electrode manufacturer.
- To do this, connect the connector of the earth terminal 4 (black) with the relevant output on the inverter welder (black, marked with “-”).
- Connect the connector of the electrode holder 5 (red) with the relevant output on the inverter welder (red, marked with “+”).
- Put on appropriate protective clothing in accordance with the specifications and prepare your workspace.
- Connect the earth terminal 4 to the workpiece.
- Clamp the electrode into the electrode holder 5 .
- Switch the device on by setting the ON/OFF switch to the 9 “I” (“ON”) position.
- Adjust the welding current using the rotary knob 2 depending on the electrode being used.
Note: See the following table for information on the welding current to be used, depending on the electrode diameter.
Ø Electrode | Welding current |
1.6 mm | 40 – 55 A |
2.0 mm | 55 – 65 A |
2.5 mm | 65 – 80 A |
3.2 mm | 80 – 120 A |
Attention: Do not bring the earth terminal 4 and the electrode holder 5 / electrodes into direct contact with one another.
Attention: When welding with electrodes (MMA – manual metal arc welding – electrode welding), the electrode holder 5 and the earth terminal 4 must be connected in accordance with the specifications of the electrodes to plus (+) or minus (-).
- Hold the welding mask 7 in front of the face and start the welding procedure.
- To stop the procedure, set the ON/ OFF switch 9 to “O” (“OFF”) position.
ATTENTION!
When the thermal sensor is triggered, the yellow control lamp 3 lights up. In this case, it will not be possible to continue welding. The device will remain in operation so that the fan can cool the device. As soon as the device is ready for operation again, the yellow control lamp 3 will switch off automatically. The
The welding function can now be used again.
ATTENTION!
Make sure that you do not rub the electrodes. Doing this can damage the workpiece and make it more difficult to ignite the arc. After the arc is ignited, maintain the correct gap from the workpiece. The distance should be appropriate to the diameter of the electrode used. When welding maintains this gap as accurately and consistently as possible. The angle between the electrode and the direction of operation should be between 20° and 30°.
ATTENTION!
The welding clamp and welding electrodes must be placed on the insulated bracket after welding. Wait until the electrode is cooled before removing the welding slag. To weld an intermittent weld seam again you must first remove the welding slag at the welding position.
ATTENTION!
A voltage that is 10% below the rated input voltage of the welding device can have the following consequences:
- The power to the device will reduce.
- The arc stops or becomes unstable.
ATTENTION!
- The arc radiation can lead to inflammation of the eyes and skin burns.
- Casting and welding slag can cause eye injuries and burns.
- Wear tinted safety goggles or a protective mask.
- The safety mask must meet the EN175 safety standards.
- It is essential that you only use the welding cable which is included with the delivery (10 mm 2 ).
Welding
Choose between push and drag welding. The following section shows the impact of the direction of movement on the properties of the weld seam:
Push welding | Drag welding | |
![]() |
![]() |
|
Burn | smaller | larger |
Weld seam width | larger | smaller |
Weld bead | flatter | higher |
Weld seam fault | larger | smaller |
Note: You decide for yourself which type of welding is most suitable, once you have welded a sample piece.
Note: Once it has worn down completely, the electrode must be replaced.
Maintenance and cleaning
Note: The welding device must be regularly serviced and overhauled for proper function and for compliance with the safety requirements. Improper and the wrong operation may cause failures and damage to the device.
- Before performing cleaning work on the welding tool, disconnect the power cable 10 from the power outlet to ensure the tool is safely isolated from the power supply.
- Clean the exterior of the welding device and its accessories regularly. Use compressed air, cotton waste or a brush to remove dirt and dust.
Note: The following kinds of maintenance work must be performed only by suitably qualified personnel.
- The current regulator, earthing device, internal cables, the coupling device of the welding torch and adjusting screws must be serviced regularly. Re-tighten loose screws and replace rusty screws (replacement M4 x 10 screws are available in any commercial hardware store).
- Check the insulation resistance levels of the welding device regularly. To do this use an appropriate measuring device.
- In case of a defect or a necessary replacement of equipment parts, please contact the appropriately qualified personnel.
Information about recycling and disposal
Don’t throw away – recycle
Please return this device, accessories and packaging to your local recycling depot.
According to European Directive 2012/19/EU, used electrical devices must be collected separately for environmentally compatible recycling or recovery. Please return this device to an approved waste management company or use your municipal waste collection service. Please ensure you comply with local regulations. If you have any questions, please contact your local authority or waste management company.
EU Declaration of Conformity
We,
C.M.C. GmbH
Responsible for documentation:
Dr Christian Weyler
Katharina-Loth-Str. 15
66386 St. Ingbert
Germany
hereby take sole responsibility for declaring that the product
Inverter welder
Art. no.: 2338
Year of manufacture: 2021/18
IAN: 337360_2007
Model: PISG 120 B3
meets the basic safety requirements as specified in the European Directives
EC low-voltage directive:
2014 / 35 / EU
EC Guideline on Electromagnetic Compatibility:
2014 / 30 / EU
RoHS directive:
2011 / 65 / EU+2015/863/EU
and the amendments to these Directives. The object of the declaration described above meets the requirements of Directive 2011/65/EU of the European Parliament and of the Council of 8 June 2011 on the restriction of the use of certain hazardous substances in electrical and electronic equipment. This conformity assessment is based on the following harmonised standards:
EN 60974-1:2018/A1:2019
EN 60974-10:2014/A1:2015
St. Ingbert, 22/10/2020
pp Dr Christian Weyler
– Quality Assurance –
Warranty and service information
Warranty from Creative Marketing & Consulting GmbH
Dear Customer,
The warranty for this equipment is 3 years from the date of purchase. In the event of product defects, you have legal rights against the retailer of this product. Your statutory rights are not affected in any way by our warranty conditions, which are described below.
Warranty conditions
The warranty period begins on the date of purchase. Please retain the original sales receipt. This document is required as your proof of purchase.
Should this product show any defect in materials or manufacture within 3 years from the date of purchase, we will repair or replace it – at our discretion – free of charge. This warranty service requires that you retain proof of purchase (sales receipt) for the defective device for the three year period and that you briefly explain in writing what the fault entails and when it occurred. If the defect is covered by our warranty, we will repair and return your product or send
you a replacement. The original warranty period is not extended when a device is repaired or replaced.
The warranty period and statutory claims for defects
The warranty period is not extended by the guarantee. This also applies to replaced and repaired parts. Any damages or defects detected at the time of purchase must be reported immediately after unpacking. Any incidental repairs after the warranty period are subject to a fee.
Extent of warranty
This device has been manufactured according to strict quality guidelines and carefully inspected before delivery. The warranty applies to material and manufacturing defects only. This warranty does not extend to product parts, which are subject to normal wear and tear and can thus be regarded as consumable parts, or for damages to fragile parts, e.g. switches, rechargeable batteries or parts made from glass.
This warranty is voided if the product becomes damaged or is improperly used or maintained. For proper use of the product, all of the instructions given in the operating instructions must be followed precisely. If the operating instructions advise you or warn you against certain uses or actions, these must be avoided in all circumstances.
The product is for consumer use only and is not intended for commercial or trade use. The warranty becomes void in the event of misuse and improper use, use of force, and any work on the device that has not been carried out by our authorised service branch.
Processing of warranty claims
To ensure prompt processing of your claim, please follow the instructions given below.
Please retain the proof of purchase and the article number (e.g. IAN) for all inquiries. The product number can be found on the type plate, an engraving, the cover page of your instructions (bottom left), or the sticker on the back or underside of the device.
In the event of malfunctions or other defects, please first contact our service department below by phone or email. If your product is found to be defective,
you can then send your product with proof of purchase (till receipt) and a statement describing what the fault involves and when it occurred free of charge to the service address given.
Note:
You can download this handbook and many more, as well as product videos and software at www.lidl-service.com.
With this QR code, you can gain immediate access to the Lidl Service page (www.lidl-service.com) and you can open your operating instructions by entering the article number (IAN) 337360.
Service
How to contact us:
GB
Name: C. M. C. GmbH
Website: www.cmc-creative.de
E-mail: [email protected]
Phone: 0-808-189-0652
Registered office: Germany
IAN 337360_2007
Please note that the following address is not a service address. Please first contact the service point given above.
Address: C. M. C. GmbH
Katharina-Loth-Str. 15
66386 St. Ingbert
GERMANY
Ordering spare parts:
www.ersatzteile.cmc-creative.de