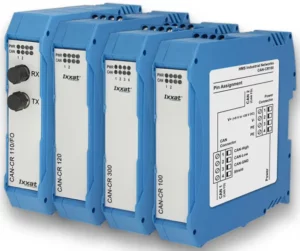
CAN FD Repeater
CAN-CR100, CAN-CR110/FO, CAN-CR120/HV, CAN-CR300
USER MANUAL
4.01.0210.20000 1.4 en-US ENGLISH
Important User Information
Disclaimer
The information in this document is for informational purposes only. Please inform HMS Industrial Networks of any inaccuracies or omissions found in this document. HMS Industrial Networks disclaims any responsibility or liability for any errors that may appear in this document.
HMS Industrial Networks reserves the right to modify its products in line with its policy of continuous product development. The information in this document shall therefore not be construed as a commitment on the part of HMS Industrial Networks and is subject to change without notice. HMS Industrial Networks makes no commitment to update or keep current the information in this document.
The data, examples, and illustrations found in this document are included for illustrative purposes and are only intended to help improve understanding of the functionality and handling of the product. In view of the wide range of possible applications of the product, and because of the many variables and requirements associated with any particular implementation, HMS Industrial Networks cannot assume responsibility or liability for actual use based on the data, examples, or illustrations included in this document nor for any damages incurred during the installation of the product. Those responsible for the use of the product must acquire sufficient knowledge in order to ensure that the product is used correctly in their specific application and that the application meets all performance and safety requirements including any applicable laws, regulations, codes, and standards. Further, HMS Industrial Networks will under no circumstances assume liability or responsibility for any problems that may arise as a result of the use of undocumented features or functional side effects found outside the documented scope of the product. The effects caused by any direct or indirect use of such aspects of the product are undefined and may include e.g. compatibility issues and stability issues.
User Guide
Please read the manual carefully. Make sure you fully understand the manual before using the product.
Target Audience
This manual addresses trained personnel who are familiar with CAN, CAN FD, and the applicable standards. The contents of the manual must be made available to any person authorized to use or operate the product.
Document History
Version | Date | Description |
1 | Feb-18 | First release |
1.1 | Feb-18 | Minor corrections |
1.2 | Mar-19 | Layout changes, added description for lock time and extending the recessive bit |
1.3 | May-19 | Corrections bit rate |
1.4 | Jul-20 | Added FO connector type to technical data and description of automatic error detection |
Trademark Information
Ixxat® is a registered trademark of HMS Industrial Networks. All other trademarks mentioned in this document are the property of their respective holders.
Conventions
Instructions and results are structured as follows:
► instruction 1
► instruction 2
→ result 1
→ result 2
Lists are structured as follows:
• item 1
• item 2
Bold typeface indicates interactive parts such as connectors and switches on the hardware, or menus and buttons in a graphical user interface.
This font is used to indicate program code and other kinds of data input/output such as configuration scripts.
This is a cross-reference within this document: Conventions, p. 4
This is an external link (URL): www.hms-networks.com
Safety advice is structured as follows:
Cause of the hazard!
Consequences of not taking remediate action. How to avoid the hazard.
Safety signs and signal words are used dependent on the level of the hazard.
This is additional information that may facilitate installation and/or operation.
This instruction must be followed to avoid a risk of reduced functionality and/or damage to the equipment or to avoid a network security risk.
Caution
This instruction must be followed to avoid a risk of personal injury.
WARNING
This instruction must be followed to avoid a risk of death or serious injury.
Safety Instructions
Information on EMC
Risk of interference to radio and television if used in office or home environment!
Make sure, that DIN rail is connected to the ground.
Use exclusively included accessories. Use exclusively shielded cables.
Make sure, that the shield of the CAN cable is connected.
If necessary, enlarge the distance between the source of interference (e.g. motors, frequency inverter) or drain of interference and device to avoid interference.
General Safety Instructions
► Protect product from moisture and humidity.
► Protect product from too high or too low temperature (see Technical Data, p. 12).
► Protect product from fire.
► Do not paint the product.
► Do not modify or disassemble the product. Service must be carried out by HMS Industrial Networks.
► Store products in dry and dust-free place.
Intended Use
The devices are used to establish a physical coupling of two or more segments of a CAN or CAN
FD bus system. It is possible to implement tree or star topologies, as well as long drop lines. With a galvanically isolated repeater network segments can be electrically decoupled. The devices cannot be used to extend a CAN/CAN FD system because in terms of signal the repeater corresponds to a line with delay time.
Scope of Delivery
Included in the scope of delivery:
• CAN FD Repeater
• User Manual CAN FD Repeater
Product Description
Features
CAN-CR100
• 2 x CAN/CAN FD interfaces according to ISO 11898-2
• ISO CAN FD and nonISO CAN FD
• variant with integrated bus termination resistor and a variant without bus termination resistor available
• 1 kV isolation voltage
CAN-CR120/HV
• 2 x CAN/CAN FD interfaces according to ISO 11898-2
• ISO CAN FD and nonISO CAN FD
• variant with integrated bus termination resistor and a variant without bus termination resistor available
• 3 kV isolation voltage
CAN-CR110/FO
• 2 x CAN/CAN FD interfaces:
– 1 x CAN interface according to ISO 11898-2
– 1 x FO interface (F-SMA connector)
• ISO CAN FD and nonISO CAN FD
• variant with integrated bus termination resistor and a variant without bus termination resistor available
• 1 kV isolation voltage
HMS Industrial Networks offers cable assemblies (F-SMA) in various lengths to connect two CAN-CR110/FO.
CAN-CR300
• 4 x CAN/CAN FD interfaces according to ISO 11898-2
• ISO CAN FD and nonISO CAN FD
• variant with integrated bus termination resistor and a variant without bus termination resistor available
• 1 kV isolation voltage
Automatic Error Detection
The Ixxat CAN FD Repeater automatically disconnects a defective segment from the network, allowing the remaining network to continue working. After successful troubleshooting, the segment is automatically reconnected.
A segment is detected as a defect and therefore disconnected if a dominant bus level is detected on the channel for more than 1.4 ms. If a recessive level is detected again on the channel, the segment is reconnected automatically.
Configuration
To operate the CAN repeater no software installation is required. The CAN repeater is configured via DIP switches (1).
Fig. 1, DIP switches
Configuring the Lock Time
The CAN transceiver transmits data and receives these transmitted data again after a certain delay, the so-called loop delay. For example, if the transceiver transmits a dominant bit and after that a recessive bit, the transceiver only sees the recessive bit in its receive output after the loop delay. The size of the loop delay depends on several factors, like for example the number of CAN nodes in the network. The higher the capacity load is, the higher is the loop delay. To avoid bit errors caused by this delay, the configured lock time must be higher than the loop delay.
► Use a screwdriver or similar tool to set the DIP switches.
► Observe, that the setting depends on the bit rate and the capacitive load of the network (the higher the capacity load, the higher the value).
► Configure the lock time with DIP switches 1 and 2.
► Observe the following reference values:
– for networks with less than 32 nodes the lock time is about 200 ns
– for networks between 32 and 64 nodes the lock time is about 400 ns
– for networks with more than 64 nodes the lock time is about 800 ns and with this setting the bit rate is limited to maximal 500 kbit/s
Valid Lock Time Combinations
DIP switch 1 | DIP switch 2 | Lock time |
Off | Off | 200 ns (default) |
On | Off | 400 ns |
Off | On | 800 ns |
On | On | 1600 ns |
Extending the Recessive Bit
Due to the internal structure, the CAN transceiver shortens recessive bits on the network, and thus dominant bits are extended. At high bit rates, this might cause errors. Extending the recessive bits may improve the error rate, as the bits are closer to their nominal value on the network. If the recessive bits are extended with the DIP switches, the extension is made independently of the bit rate, also at low bit rates.
► Use a screwdriver or similar tool to set the DIP switches.
► Extend the recessive bit with DIP switches 3 and 4.
Valid Combinations
DIP switch 3 | DIP switch 4 | Recessive bit extension |
Off | Off | 0 ns (default) |
On | Off | 10 ns |
Off | On | 20 ns |
On | On | 30 ns |
Installation
Mounting the Device
Fig. 2
Mounting on DIN rail
► Make sure that the lock time is configured (see Configuration, p. 7).
► Make sure, that the device is not connected to power supply.
► Hook the device onto the upper lip of the rail and push downwards (1).
► Push the device towards the rail until it snaps into place (2).
Connectors
Fig. 3
Connectors
1 | CAN 1 |
2 | CAN 3 |
3 | Power |
4 | CAN 2 |
5 | CAN 4 |
The CAN connectors and the power connector are fixed and can not be removed.
Power Connector
Pin Allocation
Pin no. | Signal |
1 | +9 V to +36 V DC |
2 | 0 V |
3 | — |
4 | — |
CAN Connector
Pin Allocation
Pin no. | Signal |
1 | CAN high |
2 | CAN low |
3 | CAN GND |
4 | Shield |
If a D-Sub 9 connector is used, observe the following pin allocation of the D-Sub 9 connector.
Pin no. | Signal |
1 | — |
2 | CAN low |
3 | CAN GND |
4 | — |
5 | — |
6 | — |
7 | CAN high |
8 | — |
9 | — |
The shield of the CAN connector is connected to the ground via a 10 nF capacitor. The ground of the device is connected to the DIN rail after mounting the device on the DIN rail. The ground of the CAN connector (CAN GND) is connected via a 10 nF capacitor to the device ground.
For best noise immunity, ground the shields of the CAN cables.
Operation
LEDs
LEDs PWR 2/3/4 do not have any function.
The LEDs CAN 3/4 are activated only with CAN-CR300.
Power LED
Power LED PWR 1 indicates the status of the power supply.
LED state | Description | Comments |
Off | No power | Device not connected to power supply, or fuses of device or internal power supply damaged |
Green | Power ok | Device fully functional |
Red | Device is reset | After power-up the device is set into reset, LEDs are red during reset (normal duration: about 200 ms). Or power supply is damaged, internal voltage is below necessary level. |
CAN LEDs
With CAN-CR100, CAN-CR120/HV and CAN-CR110/FO the LEDs CAN 1 and 2 indicate the status of the CAN connections.
With CAN-CR300 LEDs CAN 1, 2, 3 and 4 indicate the status of the CAN connections.
LED state | Description | Comments |
Off | No CAN communication | No CAN communication, device not connected to CAN |
Green or green flashing |
CAN communication | LED is triggered when a dominant bit is transmitted to the respective CAN port. |
Red flashing | CAN communication, but errors | Each CAN circuit transmits and reads back the transmitted bits. An error occurs, if the repeater transmits a dominant bit, but measures a recessive bit. |
Red | Dominant-lock | The external device applies a permanent dominant level to the CAN. |
Technical Data
Weight | Approx. 150 g |
Operating temperature | -20 °C to +70 °C |
Storage temperature | -40 °C to + 85 °C |
Power supply | +9 V to +36 V DC |
Housing material | Polyamide |
CAN/CAN FD transceiver | Microchip MCP2562FD |
CAN bus termination resistor | 120 Ohm (only with variants with integrated bus termination resistor) |
CAN bit rates | Up to 1 Mbit/s |
CAN FD bit rates | 500 kbit/s up to 4 Mbit/s |
Protection class | IP20 |
Relative humidity | 10 to 95 %, non-condensing |
CAN-CR100 | |
Dimensions | 22.5 x 105 x 114 mm |
Current consumption at 24 V | Typ. 70 mA, max. 100 mA |
Galvanic isolation | 1 kV DC/1 sec, 500 V AC/1 min |
CAN propagation delay (typical) | Typ. 175 ns (35 m bus length) |
CAN-CR120/HV | |
Dimensions | 22.5 x 105 x 114 mm |
Current consumption at 24 V | Typ. 70 mA, max. 100 mA |
Galvanic isolation | 3 kV DC/1 sec, 1500 V AC/1 min |
CAN propagation delay (typical) | Typ. 175 ns (35 m bus length) |
CAN-CR110/FO | |
Dimensions | 22.5 x 105 x 120 mm |
Current consumption at 24 V | Typ. 70 mA, max. 100 mA |
Galvanic isolation | 1 kV DC/1 sec, 500 V AC/1 min |
CAN propagation delay (typical) | Typ. 300 ns (60 m bus length) between wire connection of a FO Repeater through the fiber optic cable to the wired connection of a second FO Repeater (not including the signal delay time of the fiber optics: approx. 5 ns/m) |
FO transmitter | Broadcom HFBR 1404Z, 820 nm |
FO receiver | Broadcom HFBR 2402Z, 820 nm |
FO connector | F-SMA connector |
FO line | Multimode fiber optic cables (only glass); Recommended: 50/125 μm, 62.5/125 μm, also compatible with: 100/140 μm, 200 μm (consider max. line length) |
Maximal line length between two FO repeaters | 50/125 μm: 1500 m 62.5/125 μm: 2000 m |
CAN-CR300 | |
Dimensions | 22.5 x 105 x 114 mm |
Current consumption at 24 V | Typ. 90 mA, max. 125 mA |
Galvanic isolation | 1 kV DC/1 sec, 500 V AC/1 min |
CAN propagation delay (typical) | Typ. 175 ns (35 m bus length) |
Support/Return Hardware
9.1. Support
► For problems or support with the product request support at www.ixxat.com/support.
► If required use supports phone contacts on www.ixxat.com.
9.2 Return Hardware
► Fill in the form for warranty claims and repair on www.ixxat.com/support/product-returns.
► Print out the Product Return Number (PRN resp. RMA).
► Pack product in a physically- and ESD-safe way, use original packaging if possible.
► Enclose PRN number.
► Observe further notes on www.ixxat.com.
► Return hardware.
10. Disposal
► Dispose of the product according to national laws and regulations.
► Observe further notes about the disposal of products on www.ixxat.com.
Regulatory Compliance
EMC Compliance (CE)
The product is in compliance with the Electromagnetic Compatibility Directive. More information and the Declaration of Conformity is found at www.ixxat.com.
FCC Compliance Statement
This device complies with Part 15 of the FCC Rules. Operation is subject to the following two conditions:
• This device may not cause harmful interference.
• This device must accept any interference received, including interference that may cause undesired operation.
Product name: CAN Repeater
Model: CAN-CR100, CAN-CR110/FO, CAN-CR120/HV, CAN-CR300
Responsible party: HMS Industrial Networks Inc
Address: 35 E. Wacker Dr, Suite 1700, Chicago, IL 60601
Phone : +1 312 829 0601
Any changes or modifications not expressly approved by HMS Industrial Networks could void the user’s authority to operate the equipment.
This equipment has been tested and found to comply with the limits for a Class A digital device, pursuant to part 15 of the FCC Rules. These limits are designed to provide reasonable protection against harmful interference when the equipment is operated in a commercial environment. This equipment generates, uses, and can radiate radio frequency energy and, if not installed and used in accordance with the instruction manual, may cause harmful interference to radio communications. Operation of this equipment in a residential area is likely to cause harmful interference in which case the user will be required to correct the interference at his own expense.
A.3 RoHs Directive
The product is in compliance with the RoHs Directive 2002/95/EC (Restriction of the use of certain hazardous substances in electrical and electronic equipment).
A.4 Disposal and recycling
You must dispose of this product properly according to local laws and regulations. Because this product contains electronic components, it must be disposed of separately from household waste. When this product reaches its end of life, contact local authorities to learn about disposal and recycling options, or simply drop it off at your local HMS office or return it to HMS. For more information, see www.hms-networks.com.
© 2020 HMS Industrial Networks
Box 4126
300 04 Halmstad, Sweden [email protected]
4.01.0210.20000 1.4 en-US / 2020-07-15 / 19312