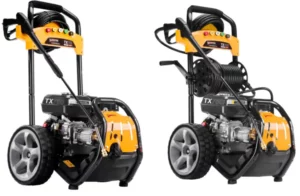
OPERATION MANUAL
TX750/TX750i
Petrol Pressure Washer
Read this manual carefully before use and keep it for future reference. Failure to do so may result in injury, and property damage and may void the warranty.
Products covered by this manual may vary in appearance, assembly, inclusions, specifications, description, or packaging.
Safety
- Always remove any excess water from the system after use to avoid freeze damage.
- Do not touch the nozzle or water spray while operating.
- Never spray directly at the pressure washer or any electrical units/wires.
- Never run the washer with damage to the high-pressure hose.
- All hose connections must be properly sealed.
- Never disconnect the high-pressure hose from the machine while the system is still pressurized.
- Never operate when there is a noticeable change in engine speed, a noticeable loss of pressure, an engine misfire, signs of smoke or fire, excessive vibration, or if there is rain or inclement weather.
- All equipment must be placed on a firm, level, and stable surface.
- Keep the pressure washer clean and free of oil, mud, and dirt.
- Be sure ice has not formed in any part of the equipment before starting.
- Wear safety goggles while operating.
- Never directly spray the hose at people or animals.
- Never allow children to operate the pressure washer at any time.
- The spray gun should be secured by locking the trigger when not in use.
- Do not run the pressure washer for more than two minutes without depressing the trigger.
- Test the pressure washer on a small inconspicuous area first. Some surfaces can be damaged by high-pressure water spray.
- Before every use, check the oil level
- Only use unleaded gasoline with an octane level over 86.
- Ensure your hose does not touch the hot exhaust during or after use.
- Ensuring the water supply is clean and free of any foreign objects.
- Inlet water temperature must not exceed 40ºC and 20 PSI.
Quick start guide
The following steps describe the quickest method to get your pressure washer up and running. However, it is essential you fully read this manual to ensure you are familiar with the general safety features, precautions, and functions necessary to operate the product. Failure to do so may result in injury and damage to your washer or personal items.
01. Nozzle panel 02. Hose reel (TX750i model) 03. Crank handle 04. Air filter 05. Exhaust 06. Detergent tank |
07. Pump 08. On/Off switch 09. Fuel tank 10. Hun hook 11. Handle section |
Assembly
![]() |
||
Locate the axle holes on the underside of the frame. Insert the axle so the sprung clip locks in place | Slide the wheel over the axle and secure it with the nut. | For TX750i model only: Slide the hose reel and bracket over the handle section and secure with four nuts and bolts taking care not to over-tighten the brackets. Attach the crank handle |
![]() |
||
Push the handle in place by inserting both sides evenly into the frame so the sprung catches click into the holes | The nozzle panel is fixed in place with four long nuts and bolts |
Before starting
Note: the washer will automatically shut down if insufficient oil is detected.
![]() |
|
Add fuel: 01. Open the filler cap 02. Fill with unleaded petrol up to the filter 03. Replace filler cap |
Add oil: 01. Locate the filler bungs on either side of the engine 02. Place washer on a level surface 03. Open the oil filler bung 04. Fill with 10W-40 semi-synthetic oil up to the threads 05. Replace oil filler bung |
Connections
01. Connect the high-pressure hose to the gun ‘A’
02. TX750: Connect the high-pressure hose to pump ‘B’
03. TX750i: Connect the high-pressure hose to the reel ‘D’ and the reel hose to ‘B’
04. Connect a mains supply hose to the water inlet ‘C’
Starting
Before starting, connect the gun and hoses as described in ‘Connections’
![]() |
||
Turn the fuel tap on by sliding to the right | Set the choke to the left (closed position) | Turn the engine switch to the on position |
![]() |
||
Pull the recoil handle firmly to start the engine | Once running pull the throttle to the left (open position) | Turn on the water supply |
Once running and the engine has warmed up, return the choke to the right (open) position.
If restarting a warm engine there is no need to move to the left.
Stopping
![]() |
||
Turn the engine switch to the off position | Turn the fuel tap off by sliding to the left | Turn the water supply off |
Note: make sure you depress the trigger on the gun to fully drain any residual water left in the system.
Failure to do so can result in damage due to corrosion or water expansion when freezing.
Using detergent
- Open the front cap on the detergent tank and fill it with a suitable pressure washer detergent. Do not use the washing-up liquid as it contains salt.
- Fit the blue/black nozzle to the end of the lance.
- Suction and mixing will occur as the water flows through the pump. You may be required to fit the shorter of the supplied hoses in conjunction with the blue/black nozzle to create the required pressure to draw detergent.
Note: a thick viscous detergent will not flow freely from the detergent tank and the residue is likely to cause a blockage in the system. After using the detergent facility it should be flushed thoroughly with clean water to remove any trace of detergent.
Drawing from a barrel
First, ensure the machine is switched off before connecting/disconnecting any hoses or attachments. Instead of attaching the hose from the pump to the tap, use the supplied hose and filter set placing the filter end in the water supply.
It is advised that the water supply is on the same level as the washer. If you struggle to get initial suction, remove the outlet hose from the pump and try drawing again – this reduces the pressure on the pump making it easier to draw. Once flowing, turn the engine off and reconnect the outlet hose before re-starting.
Nozzles
0°Nozzle (Red) Fig 1 – This nozzle delivers a pinpoint stream of pressurized water and is extremely powerful. It should only be directed at surfaces that can withstand high pressure such as metal or concrete.
15° Nozzle (Yellow) Fig 2 – This nozzle delivers a powerful 15-degree spray pattern for intense cleaning of small areas. This nozzle should only be used on areas and materials that can withstand very high pressure.
25° Nozzle (Green) Fig 3 – This nozzle delivers a 25-degree spray pattern for intense cleaning of larger areas. This nozzle should only be used on areas that can withstand very high pressure.
40° Nozzle (White) Fig 4 – This nozzle delivers a 40-degree spray pattern and a less powerful stream of water. This nozzle can cover a wide area and can be used for most general cleaning jobs.
Detergent Nozzle (Blue/Black) Fig 5 – This nozzle is used to apply detergent and cleaning solutions.
This nozzle produces the weakest pressure of the three nozzles.
Maintenance
Spark plug
![]() |
||
Remove the spark plug cap | unscrew the spark plug using the supplied tool | Check the gap using a gauge. The gap should be between 0.7-and 0.8mm. |
Oil change
![]() |
||
Locate and remove either of the oil bungs on the side of the engine | Place a pan under one side and tilt the unit to drain the oil | Add 10W-40 semi-synthetic oil to the upper limit of the filler hole |
Air filter
The air filter is installed on the intake system of the engine. It allows clean air to flow into the engine to provide the correct air/fuel mixture.
- Lift the clip to open-air filter cover
- Check the air filter to ensure it is free of dirt build-up
- If dirty, remove the filter and clean with a solvent cleaning solution
- Squeeze to remove water and allow to dry
- Add a few drops of oil
- Squeeze tight to distribute oil and remove any excess
- Install air filter and cover
Service schedule
Component/Task | Every Use | After the First 5 Hours Use | After First Month or 20 Hours Use | Every 3 Months or 50 Hours Use | Every 6 Months or 100 Hours Use | Every Year or 300 Hours Use |
Engine Oil | Check | Replace | Replace | |||
Oil Leaks | Check/repair as necessary | |||||
Air Filter | Check | Clean | Clean and replace as necessary | Clean and replace as necessary | ||
Valve Clearance | Adjust as necessary | |||||
Combustion Chamber | De-coke as necessary | |||||
Idle Speed | Check/adjust as necessary | |||||
Nuts & Bolts | Check/tighten as necessary | |||||
Fuel Tank | Flush and clean | |||||
Fuel Line | Check | Check/ Clean | Clean and replace as necessary | Clean and replace as necessary | ||
Fuel Filter | Check | Check/ Clean | Clean and replace as necessary | Clean and replace as necessary | ||
Spark Plugs | Check/ Clean | Clean and replace as necessary | Clean and replace as necessary |
Storage
If the washer is not to be used or is to be stored for more than one month the following storage procedure should be carried out:
- Drain all the fuel from the fuel tank and the carburetor. Ensure that all fuel has been removed.
- Remove the spark plug and pour approximately one tablespoon full of clean engine oil into the spark plug hole.
- With the ignition turned OFF, gently pull on the recoil starter handle several times.
- Re-fit the spark plug and continue to pull the recoil starter handle until the piston is on the compression stroke (when resistance is felt) then stop pulling.
- Store the pressure washer in a dry well ventilated place under a cover to prevent any dust or debris from accumulating on the pressure washer.
If the pressure washer is not being used for more than three months or if there is any danger of ice or frost where the unit is stored, especially during the winter months, certain precautions must be taken to ensure no damage occurs to your washer or gun. Follow the previous steps for storage but also ensure there is no water left inside the unit. The pump may require insulated protection from freezing conditions. The gun must be drained of fluids to avoid water expansion as this will damage your gun.
Removal from storage
No fuel should have been left in the unit. However if any fuel is present, ensure this is removed from the tank and carburetor before refueling with fresh fuel. Check the deposit cup and empty it if necessary.
Note: old fuel will not combust correctly and could damage your engine.
Troubleshooting
Fault | Probable Cause | Remedy | ||
Fluctuating Pressure | Pump sucking in air | Check connections are tight | ||
Blocked jet | Remove blockage using a jet cleaning tool | |||
The pump does not reach the required pressure | Pump sucking in air from connections or hose | Check connections are tight | ||
Suction/delivery valves are clogged | Clear or replace valves. Have the machine checked by a service center | |||
Unload valves are stuck | Loosen and re-tighten regulating screw | |||
Lance or nozzle is worn out | Check and/or replace | |||
The pump is running but no water delivery | Kinked inlet and or pressure hose | Check, straighten and replace if required | ||
Blocked inlet filter | Remove and clean the filter | |||
Blocked jet | Remove blockage using jet cleaning tool | |||
The engine won’t start Low engine output Engine runs erratically |
Insufficient compression | Loose spark plug | Tighten plug | |
Loose cylinder head bolt | Tighten bolt | |||
Damaged gasket | Replace gasket | |||
Sufficient compression | Fuel System Problems | |||
No fuel is supplied to the combustion chamber | Insufficient pulling speed for recoil starter | Pull rope sharply | ||
Foreign matter in the fuel tank | Clean tank | |||
Clogged fuel line | Clean fuel line | |||
No fuel in the tank | Add fuel | |||
The fuel tap is not open | Open fuel cap | |||
Combustion System Problems | ||||
Combustion chamber (Poor spark) | Spark plug dirty with carbon or wet with fuel | Remove carbon or dry spark plug | ||
Damaged spark plug | Replace spark plug | |||
Faulty magneto | Consult dealer | |||
Combustion chamber (Good spark) | Improper adjustment of the carburetor | |||
Insufficient oil | On a level surface, ensure oil is topped up to the filler threads |
Specifications
Max pressure (PSI / BAR) | 3950 / 272 |
Working pressure (PSI / BAR) | 3200 / 220 |
Flow rate (Litres per minute) | 660 |
Engine power (HP) | 8 |
Engine type | 4-stroke OHV |
Starting system | Recoil |
Oil type | 10W-40 semi-synthetic |
Fuel type | Unleaded 95+ |
Dimensions L x W x H (CM) | 65 x 41 x 52 |
Weight (KG) | 29.5 |
CE declaration of conformity
We hereby certify that the machine detailed below complies with all relevant provisions of the EC Machinery Directive 2006/42/EC and National Laws and Regulations adopting this Directive.
Declaration Ref. No.: | TX750 / TX750i |
Manufacturer: | Union Mart |
Manufactures Address: | Unit 4, Mauretania Rd, Nursling Industrial Estate, Nursling, Southampton SO16 0YS, |
Authorized Representative (in EU): | Union Mart Ltd |
Authorized Representative’s Address: | Unit 4, Mauretania Rd, Nursling Industrial Estate, Nursling, Southampton SO16 0YS, UK |
Name of the person authorized to compile the technical file (in EU): |
Michael S McQuaide |
Address of the person authorized to compile the technical file (in EU): | Unit 4, Mauretania Rd, Nursling Industrial Estate, Nursling, Southampton SO16 0YS, UK |
Product: | Petrol Pressure Washer Wilks-USA TX750 / TX750i |
Description: | Petrol High-Pressure Washer |
Type / Model No.: | Wilks-USA TX750 / TX750i |
Procedure for assessment of conformity conducted by: |
ISET S.r.l. Sede Legale e Uffici (Note: Machinery is NOT referred to in Annex IV) |
We hereby declare that the machine detail also complies with all relevant provisions of the following other EC Directives: | 2006/42/EC Machinery Directive 2000/14/EC Noise Emission 2014/30/EU EMC Directive |
Harmonized Standards Applied (in full): | EN 60335-2-79:2012 EN 1679-1:1998+A1:2011 EN 55012:2007/A1:2009 |
A person empowered to draw up the declaration: | Michael S McQuaide |
Signature: | ![]() |
Date: | 15.08.2018 |
Position: | Managing |
Place of issue: | Unit 4, Mauretania Rd, Nursling Industrial Estate, Nursling, Southampton SO16 0YS, UK |
This declaration relates exclusively to the machinery in the state in which it was placed on the market, and excludes components that are added and/or operations carried out subsequently by the final user