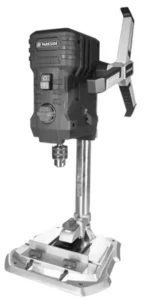
BENCH PILLAR DRILL PTBMOD 710 B2
BENCH PILLAR DRILL
Operating and Safety Instructions
Translation of Original Operating ManualBefore reading, unfold the page containing the illustrations and familiarise yourself with all functions of the device.
Operating and Safety Instructions
1. Explanation of the symbols on the device
![]() |
Warning! Non-adherence poses a risk of death, the danger of injury, or the risk of damage to the tool! |
![]() |
Before commissioning, read and observe the operating manual and safety instructions! |
![]() |
Wear safety goggles! |
![]() |
Wear hearing protection! |
![]() |
If dust builds up, wear respiratory protection! |
![]() |
Do not leave long hair loose. Use a hairnet. |
![]() |
Do not wear gloves. |
![]() |
Protection class II (double shielded) |
![]() |
Attention! Laser beam |
Introduction
MANUFACTURER:
scheppach
Fabrikation von Holzbearbeitungsmaschinen GmbH
Günzburger Straße 69
D-89335 Ichenhausen
DEAR CUSTOMER,
We hope your new tool brings you much enjoyment and success.
NOTE:
In accordance with the applicable product liability laws, the manufacturer of this device assumes no liability for damage to the device or caused by the device arising from:
- Improper handling
- Failure to comply with the operating instructions.
- Repairs are carried out by third parties, unauthorized specialists.
- Installing and replacing non-original spare parts,
- Improper use
- Failures of the electrical system in the event of the electrical regulations and VDE provisions 0100, DIN 57113 / VDE0113 not being observed.
Note: Read the whole text of the operating manual before assembly and commissioning.
This operating manual should help you to familiarise yourself with your device and to use it for its intended purpose.
The operating manual includes important instructions for the safe, proper, and economic operation of the device, for avoiding danger, for minimizing repair costs and downtimes, and for increasing the reliability and extending the service life of the device.
In addition to the safety instructions in this operating manual, you must also observe the regulations applicable to the operation of the device in your country.
Keep the operating manual at the device, in a plastic sleeve, protected from dirt and moisture. They must be read and carefully observed by all operating personnel before starting the work.
The device may only be used by personnel who have been trained to use it and who have been instructed with respect to the associated hazards. The required minimum age must be observed. In addition to the safety instructions in this operating manual and the separate regulations of your country, the generally recognized technical rules relating to the operation of such machines must also be observed.
We accept no liability for accidents or damage that occur due to a failure to observe this manual and the safety instructions.
Device description (fig. 1-11
- Base plate
- Quick clamp
- Column
- Toothed rack for height adjustment
- Clamping lever for height adjustment
- Clamping lever for depth stop
- Depth stop
- Handle
- Pointer, depth stop
- Off switch
- On switch
- Speed control
- Spacer
- Chuck
- Wing screws for parallel stop
- Parallel stop
- Quick-clamp screw
- Laser ON/OFF switch
- Phillips screw (pointer)
- Scale
- Allen key, 4 mm
- Chuck key
- Marking
Scope of delivery
- 1 Drilling machine
- 1 Quick clamp (2)
- 1 Base plate (1)
- 1 Parallel stop (16)
- 1 Spacer (13)
- 1 handle (8)
- 1 Depth stop (7)
- 1 Clamping lever (6)
- 1 Allen key, 4 mm (21)
- 1 Chuck key (22)
- 1 Operating manual
- 1 Assembly material
Proper use
The bench drill is designed for drilling in metal, wood, plastic, and tiles.
Chuck clamping range: 1.5 – 13 mm.
The device is only intended to be used for DIY purposes. It was not designed for continuous commercial use. The device is not intended for use by people under the age of 16. Children under the age of 16 may only use the device when supervised.
The manufacturer is not liable for damage caused by improper use or incorrect operation.
Please observe that our equipment was not designed with the intention of use for commercial or industrial purposes. We as- some no guarantee if the equipment is used in commercial or industrial applications, or for equivalent work.
Safety instructions
General power tool safety warnings
WARNING! Read all safety warnings, instructions, illustrations, and specifications provided with this power tool.
Failure to follow all instructions listed below may result in electric shock, fire, and/or serious injury.
Save all warnings and instructions for future reference. The term “power tool” in the warnings refers to your mains-operated (corded) power tool or battery-operated (cordless) power tool.
Work area safety
a) Keep the work area clean and well-lit.
Cluttered or dark areas invite accidents.
b) Do not operate power tools in explosive atmospheres, such as in the presence of flammable liquids, gases, or dust. Power tools create sparks that may ignite dust or fumes.
c) Keep children and bystanders away while operating a power tool. Distractions can cause you to lose control.
Electrical safety
a) Power tool plugs must match the outlet. Never modify the plug in any way. Do not use any adapter plugs with earthed (grounded) power tools. Unmodified plugs and matching outlets will reduce the risk of electric shock.
b) Avoid body contact with earthed or grounded surfaces, such as pipes, radiators, ranges, and refrigerators. There is an increased risk of electric shock if your body is earthed or grounded.
c) Do not expose power tools to rain or wet conditions. Water entering a power tool will increase the risk of electric shock.
b) Do not abuse the cord. Never use the cord for carrying, pulling, or unplugging the power tool. Keep cord away from heat, oil, sharp edges, or moving parts. Damaged or entangled cords increase the risk of electric shock.
e) When operating a power tool outdoors, use an extension cord suitable for outdoor use. Using a cord suitable for outdoor use reduces the risk of electric shock.
f) If operating a power tool in a damp location is unavoidable, use a residual current device (RCD) protected supply. The use of an RCD reduces the risk of electric shock.
Personal safety
a) Stay alert, watch what you are doing, and use common sense when operating a power tool. Do not use a power tool while you are tired or under the influence of drugs, alcohol, or medication. A moment of inattention while operating power tools may result in serious personal injury.
b) Use personal protective equipment. Always wear eye protection. Protective equipment such as a dust mask, non-skid safety shoes, hard hat, or hearing protection used for appropriate conditions will reduce personal injuries.
c) Prevent unintentional starting. Ensure the switch is in the off-position before connecting to a power source and/or battery pack, picking up or carrying the tool. Carrying power tools with your finger on the switch or energizing power tools that have the switch on invites accidents.
d) Remove any adjusting key or wrench before turning the power tool on. A wrench or a key left attached to a rotating part of the power tool may result in personal injury.
e) Do not overreach. Keep proper footing and balance at all times. This enables better control of the power tool in unexpected situations.
f) Dress properly. Do not wear loose clothing or jewelry. Keep your hair and clothing away from moving parts. Loose clothes, jewelry, or long hair can be caught in moving parts.
g) If devices are provided for the connection of dust extraction and collection facilities, ensure these are connected and properly used. The use of dust collection can reduce dust-related hazards.
h) Do not let familiarity gained from frequent use of tools allow you to become complacent and ignore tool safety principles. A careless action can cause severe injury within a fraction of a second.
Power tool uses and cares
a) Do not force the power tool. Use the correct power tool for your application. The correct power tool will do the job better and safer at the rate at which it was designed.
b) Do not use the power tool if the switch does not turn on and off. Any power tool that cannot be controlled with the switch is dangerous and must be repaired.
c) Disconnect the plug from the power source and/or remove the battery pack, if detachable, from the power tool before making any adjustments, changing accessories, or storing power tools. Such preventive safety measures reduce the risk of starting the power tool accidentally.
d) Store idle power tools out of the reach of children and do not allow persons unfamiliar with the power tool or these instructions to operate the power tool. Power tools are dangerous in the hands of untrained users.
e) Maintain power tools and accessories. Check for misalignment or binding of moving parts, breakage of parts, and any other condition that may affect the power tool’s operation. If damaged, have the power tool repaired before use. Many accidents are caused by poorly maintained power tools.
f) Keep cutting tools sharp and clean. Properly maintained cutting tools with sharp cutting edges are less likely to bind and are easier to control.
g) Use the power tool, accessories and tool bits, etc. in accordance with these instructions.
h) Keep handles and grasping surfaces dry, clean, and free from oil and greases, taking into account the working conditions and the work to be performed. Use of the power tool for operations different from those intended could result in a hazardous site. Slippery handles and grasping surfaces do not allow for safe handling and control of the tool in unexpected situations.
Service
a) Have your power tool serviced by a qualified repair person using only identical replacement parts. This will ensure that the safety of the power tool is maintained.
Drill safety warnings
a) The drill must be secured. An incorrectly secured drill can move or topple and this can result in injuries.
b) The workpiece must be clamped or fastened to the workpiece support. Do not drill into workpieces that are too small to be securely clamped. Holding the workpiece by hand can lead to injuries.
c) Do not wear gloves. Gloves can be caught by rotating parts or drilling debris and thus cause injuries.
d) Keep your hands away from the drilling area whilst the electrical tool is running. Contact with rotating parts or drilling debris can cause injuries.
e) The drill must be turning before it makes contact with the workpiece. Otherwise, the drill bit can catch in the workpiece and this can result in an unexpected movement of the workpiece and cause injuries.
f) If the drill becomes jammed, stop pressing downwards and switch the electrical tool off. Investigate and rectify the cause of the jamming. Jamming can result in an unexpected movement of the workpiece and can result in serious injuries.
g) Avoid long pieces of drill swarf by interrupting the downward pressure at regular intervals. Sharp metal swarf can become tangled and lead to injuries.
h) Never remove drilling debris from the drilling area whilst the electrical tool is running. To remove the swarf, move the drill away from the workpiece, switch off the electrical tool and wait until the drill has come to a standstill. Use an aid such as a brush or a hook to remove the swarf. Contact with rotating parts or drilling debris can cause injuries.
i) The permissible rotational speed for drill bits with a rated speed must be at least as high as the highest speed cited on the electrical tool. Accessories that rotate faster than permitted can break and fly off at high speed.
Attention: Laser radiation Do not look into the beam Laser class 2
Protect yourself and your environment from accidents using suitable precautionary measures
Do not look directly into the laser beam with unprotected eyes.
- Never look into the path of the beam.
- Never point the laser beam towards reflecting surfaces and persons or animals. Even a laser beam with a low output can cause damage to the eyes.
- Caution – methods other than those specified here can result in dangerous radiation exposure.
- Never open the laser module. Unexpected exposure to the beam can occur.
- The laser may not be replaced with a different type of laser.
- Repairs of the laser may only be carried out by the laser manufacturer or an authorized representative.
- Labeling and placement of warning stickers, see fig. 8 and9.
WARNING! This electric tool generates an electromagnetic field during operation. This field can impair active or passive medical implants under certain conditions. In order to prevent the risk of serious or deadly injuries, we recommend that persons with medical implants consult with their physician and the manufacturer of the medical implant prior to operating the electric tool.
Residual risks
Even when this electric tool is operated properly, residual risks still remain. The following hazards may arise in connection with the design and construction of this electric tool:
- Lung damage if a suitable dust protection mask is not worn.
- Hearing damage if suitable hearing protection is not worn.
- Damage to health resulting from hand/arm vibration if the device is used over an extended period of time or if it is not properly operated and maintained.
Technical data
AC motor…………………………………………….220 – 240 V~50 Hz
Nominal power S1 ……………………………………………… 710 Watt
Operating mode ………………………………………..S2 5min* 900W
Idle speed n0 …………………………………………….500 – 2600 min-1
Drill chuck clamping range ……………………………….1.5 – 13 mm.
Max. drill stroke………………………………………………………..70 mm
Size of base plate ………………………………………..320 x 305 mm
Distance chuck to bottom plate ………………………………. 280 mm
Weight approx. …………………………………………………………8,3 kg
Protection class …………………………………………………………. II /
Laser class ……………………………………………………………………….. 2
Laser wavelength ……………………………………………………. 650 nm
Laser power ……………………………………………………………< 1 mW
* After an uninterrupted operating period of 5 minutes, the device should be allowed to rest until its temperature has dropped to within 2 K (2° C) of room temperature.
The workpiece must have a minimum height of 3 mm and a minimum width of 45 mm. Make sure that the workpiece is always secured with the clamping device. Overhanging workpieces may have to be supported laterally by additional supports.
Noise
The noise levels have been determined in accordance with EN 62841.
Sound pressure level LpA …………………………………….. 89,6 dB(A)
Uncertainty KpA …………………………………………………………….3 dB
Sound power level LWA ……………………………………..102,6 dB(A)
Uncertainty KWA ……………………………………………………………3 dB
Wear hearing protection.
Excessive noise can result in a loss of hearing.
The above-mentioned noise emission values were measured in accordance with a standardised test procedure and can be used to compare one power tool with another. The pecified device emissions values can also be used for an initial estimation of the load.
Warning:
- The noise emission values can vary from the specified values during the actual use of the electric tool, depending on the type and the manner in which the electric tool is used, and in particular the type of workpiece being processed.
- Try to keep the stress as low as possible. For example, Limit working time. In doing so, all parts of the operating cycle must be taken into account (such as times in which the electric tool is switched off or times in which it is switched on, but is not running under a load).
Before commissioning
- Open the packaging and carefully remove the device.
- Remove the packaging material as well as the packaging and transport bracing (if available).
- Check whether the scope of delivery is complete.
- Check the device and accessory parts for transport damage.
- If possible, keep the packaging until the expiry of the warranty period.
ATTENTION
The device and the packaging are not children‘s toys! Do not let children play with plastic bags, films or small parts! There is a danger of choking or suffocating!
Before connecting the machine, make certain that the data on the type plate matches with the mains power data.
- Check the device for transport damage. Immediately report any damage to the transport company that delivered the electrical tool.
- Long supply cables (extension cable) should be avoided.
- Do not operate the electrical tool in damp or wet areas.
- Operate the electrical tool only in suitable areas (well ventilated).
Assembly
Attention!
Always make sure the device is fully assembled before com-missioning!
Before connecting the machine to the mains power, make certain that the data on the type plate matches with the mains power data.
Warning! Always pull out the mains plug before carrying out adjustments on the device.
9.1 Assembling the base plate and column (fig. 2)
- Slide the quick clamp (2) over the column (3).
- Set the column (3) into the base plate (1) such that the guide pins on the bottom end of the column (3) engage with the groove in the mount on the base plate (1).
- Tighten the pre-assembled fastening screws (A) on the rear of the base plate (1) with the Allen key (21).
9.2 Fitting the parallel stop (fig. 4)
- Slide the parallel stop (16) into the grooves in the base plate (1).
- Ensure that the sliding blocks underneath the wing screws of the parallel stop (15) are properly engaged in the grooves of the base plate.
- Move the parallel stop (16) to the desired position and tighten the wing screws of the parallel stop (15) firmly.
9.3 Assembling the handle (fig. 2)
- Remove the pre-assembled fastening screw (B).
- Ensure that the spacer (13) is seated correctly.
- Slide the handle (8) onto the retainer (G) as shown in fig. 2.
- Place the nut (C) in the recess in the handle (8) and tighten the fixing screw (B).
9.4 Fitting the depth stop (fig. 2)
- Insert the depth stop (7) from above into the recess in the housing.
- Assemble the clamping lever for depth stop (6) as shown in fig. 2.
9.5 Fastening to a work surface (fig. 4)
Fasten the device to the work surface by bolting the base plate
(1) to the work surface.
Operation
10.1 Height adjustment (fig. 2, 3)
The position of the machine head can be adjusted to suit the workpiece height or the workpiece length.
- Hold the handle (8) firmly.
- Release the clamping lever for the height adjustment (5).
- Set the position of the machine head with the handle (8).
- Secure the position of the machine head with the height adjustment clamping lever (5).
Attention! In the lowest position of the machine head make sure that it does not move beyond the marking (23).
Use the clamping lever for height adjustment (5) to secure the machine head in this position. Otherwise, the guide could be damaged.
10.2 Setting the drilling depth (fig. 1, 11)
The drilling depth can be set with the depth stop (7).
- Release the clamping lever on the depth stop (6).
- Carry out a test drilling. Once the desired depth is reached, tighten the depth stop clamping lever (6) again.
- The depth stop (7) is now locked in the desired drilling depth.
- Then check the position of the depth stop. If the indicated dimension does not correspond to the actual drilling depth, the pointer (9) can be readjusted.
• Loosen the Phillips screw (19) on the pointer (9).
• Set the pointer (9) to the correct position to the scale (20).
• Re-tighten the Phillips screw (19).
10.3 Clamping/releasing tools (fig. 5, 6) Caution! Do not leave the chuck key in the clamp hole. Doing so will cause the chuck key to be catapulted out, which could cause injury.
10.3.1 Clamping
- Insert the chuck key (22).
- Turn the chuck key (22) counterclockwise to open the clamping sleeve (D).
- Insert the insert tool (E).
- Hold the insert tool (E) in place.
- Turn the chuck key (22) clockwise to close the clamping sleeve (D) and to secure the insert tool.
- Check that the insert tool (E) is tight.
- Pull out the chuck key (22).
10.3.2 Releasing
- Insert the chuck key (22).
- Turn the chuck key (22) counterclockwise until the drill bit (E) can be removed.
- Pull out the chuck key (22).
10.4 Aligning workpieces (fig. 1)
- Switch on the laser cross using the On/off switch laser (18).
- The intersection of the two laser lines exactly indicates the centre point of the drill.
- Align your marking on the workpiece with the laser cross.
10.5 Clamping the workpiece (fig. 7)
It must be possible to clamp the workpiece securely. Do not work with workpieces that cannot be clamped securely.
The cut-out of the quick clamp must be centrally aligned with the hole to be drilled. Otherwise, the drill bit or the chuck could be obstructed by the quick clamp.
- Position the workpiece with the help of the laser cross.
- Loosen the quick clamp screw (17).
- Place the quick clamp (2) on the workpiece.
- Turn the quick clamp screw (17) clockwise to clamp the workpiece.
- Turn the quick clamp screw (17) anticlockwise to loosen the quick clamp (2).
10.6 Clamping larger workpieces (fig. 7)
Use the parallel stop (16) for larger workpieces:
- Loosen the wing screws for the parallel stop (15) and insert the parallel stop (16) into the grooves of the base plate.
- Tighten the wing screws for the parallel stop (15).
- Align your workpiece against the parallel stop (16) and clamp it with the quick clamp (2).
Warning! With workpieces that are wider or longer than the tabletop, ensure that these are adequately supported, e.g. through trestles or saw horses.
Workpieces that are longer or wider than the base plate of the tabletop drill can tip if they are not properly supported. If the workpiece tips, this can damage the chuck guard or the cutting tool.
10.7 Setting the drilling speed (fig. 1)
The correct speed must be set to suit the workpiece to be drilled and the tool diameter.
10.7.1 Electronic speed control
Use the electronic speed control to steplessly set the speed: Set the speed with the help of the speed control (12). The current speed can be seen using the mark on the speed control (12).
10.8 Switching on/off (fig. 1)
Switching on: Press the on switch (11) to switch the device on.
Switching off: Press the off switch (10) to switch the device off.
10.9 Drilling procedure (fig. 1, 7)
- Align the workpiece and clamp it.
- Start the device and set the speed.
- For drilling, move the handle (8) with uniform feed until the desired drilling depth is reached. When drilling into metal, interrupt the downward pressure briefly to break the swarf.
- After reaching the drilling depth, return the handle (8) to the starting position.
- Switch the device off.
Transport
Warning! Unplug the mains plug prior to transpor• To transport the device hold it by the base plate (1).
Cleaning and maintenance
Warning! Pull out the mains plug before carrying out anadjustments, maintenance or repair work!
12. 1 General maintenance tasks
Have tasks that are not described in this opering manual performed by a specialist workshop.Use only original parts. Let the device cool down
before all maintenance and cleaning tasks.
There is a risk of burn!
Before using the device each time, check the device for obvious defects such as worn or damaged parts, correct seating of screws or other parts. Replace damaged parts.
12.2 Cleaning
Do not use cleaning agents or solvents. Chemical substances could damage the plastic parts of the device. Never clean the device under running water.
- Clean the device thoroughly after each use.
- Clean the ventilation holes and the surface of the device with a soft brush or cloth.
- Remove swarf, dust and dirt with a vacuum cleaner if necessary.
- Lubricate the moving parts regularly.
12.3 Maintenance
The device has no parts that require maintenance.
12.4 Replacing the chuck (fig. 1, 5, 10)
Warning! Pull out the mains plug!
Tools required (not included in the scope of delivery):
1x open-ended wrench 27 mm
- Remove the insert tool as described in 10.3.2.
- Tighten the clamping sleeve (D) firmly by turning the chuck key (22) clockwise.
- Hold the chuck (14) with one hand while using the openended wrench (27 mm) to lower the nut (F) clockwise.
- Once the chuck (14) is loosened from the shaft seat, it can be removed.
- Fasten the new chuck in reverse order. When replacing the chuck, use only chucks approved by the manufacturer.
Order number: 390 6814 001
12.5 Service information
With this product, it is necessary to note that the following parts are subject to natural or usage-related wear, or that the following parts are required as consumables. Wear parts*: Carbon brushes, drill bit * may not be included in the scope of supply!
Storage
Store the device and its accessories in a dark, dry and frosfree place that is inaccessible to children. The optimum storage temperature lies between 5 and 30 °C. Store the electric ool in its original packaging. Cover the electric tool to protect it from dust or moisture. Store the operating manual with the electric tool.
Electrical connection
The electrical motor installed is connected and ready for operation. The connection complies with the applicable VDE and DIN provisions. The customer‘s mains connection s well as the extension cable used must also comply with these regula- tions.
14.1 Important information
In the event of overloading, the motor will switch itself off. After a cool-down period (time varies) the motor can be switched back on again.
14.2 Faulty power supply cables
The insulation on electrical connection cables is often damaged. This may have the following causes:
- Pressure points, where connection cables are passed through windows or doors.
- Kinks where the connection cable has been improperly fastened or routed.
- Places where the connection cables have been cut due to being driven over.
- Insulation damage due to being ripped out of the wall outlet.
- Cracks due to the insulation ageing.
Such damaged electrical connection cables must not be used and are life-threatening due to the insulation damage.
Check the electrical connection cables for damage regularly. Ensure that the connection cables are disconnected from electrical power when checking for damage.
Electrical connection cables must comply with the applicable VDE and DIN provisions. Only use connection cables with the marking H05VV-F. The printing of the type designation on the connection cable is mandatory.
If it is necessary to replace the connection cable, this must be done by the manufacturer or their representative to avoid safety hazards.
14.3 AC motor
The mains voltage must be 220 – 240 V~ 50Hz.
• Extension cables up to 25 m long must have a cross-section of 1.5 mm2
.Connections and repair work on the electrical equipment may only be carried out by electricians.
Please provide the following information in the event of any enquiries:
• Type of current for the motor
• Engine data – type plate
Disposal and recycling
The device is supplied in packaging to avoid transport damages. This packaging is raw material and can thus be used again or can be reintegrated into the raw material cycle. The device and its accessories are made of different materials, such as metals and plastics. Take defective components to special waste disposal sites. Check with your specialist dealer or municipal administration!
Do not throw old equipment away with household waste!
This symbol indicates that this product must not be disposed of in household waste as per Waste Electrical and Electronic Equipment directive (2012/19/EU) and national laws. This product must be handed over at the intended collection point. This can be done, for example, by returning it when purchasing a similar product or delivering it to an authorised collection point for the recycling of old electrical and electronic devices. Improper handling of old devices can have negative effects on the environment and on human health due to potential hazardous materials which are often contained in old electrical and electronic devices. By disposing of this product properly, you are also contributing to the effective use of natural resources. Information about collection points for old devices can be found at your municipal authority, the local disposal provider, an authorised location for the disposal of old electrical and electronic devices or your waste collection service.
Troubleshooting
Fault | Possible cause | Remedy |
Device does not start | Motor, cable or plug defective, building circuit breaker tripped | Check power outlet, mains connection cable, mains plug. Have repair carried out by electrical specialist. Check building circuit breakers. |
On/off switch (11/10) defective | Repair by customer service department | |
Motor defective | Repair by customer service department | |
Heavy vibrations | Base plate (1) not fastened in place. | Secure machine to a work bench or similar |
Drill bit not clamped centrally | Check drill bit in chuck (14) | |
Motor overheats easily | Overloading of the motor, insufficient cooling of the motor. | Avoid overloading the motor while drilling,
remove dust from the motor in order to ensure optimal cooling of the motor. |
Motor makes excessive noise | Coils damaged, motor defective. | Have checked by customer service department |
Warranty certificate
Dear Customer,
All of our products undergo strict quality checks to ensure that they reach you in perfect condition. In the unlikely event that your device develops a fault, please contact our service department at the address shown on this guarantee card. Of course, if you would prefer to call us then we are also happy to offer our assistance under the service number printed below. Please note the following terms under which guarantee claims can be made:
- These guarantee terms cover additional guarantee rights and do not affect your statutory warranty rights. We do not charge you for this guarantee.
- Our guarantee only covers problems caused by material or manufacturing defects, and it is restricted to the rectification of these defects or replacement of the device. Please note that our devices have not been designed for use in commercial, trade or industrial applications. Consequently, the guarantee is invalidated if the equipment is used in commercial, trade or industrial applications or for other equivalent activities. The following are also excluded from our guarantee: compensation for transport damage, damage caused by failure to comply with the installation/assembly instructions or damage caused by unprofessional installation, failure to comply with the operating instructions (e.g. connection to the wrong mains voltage or current type), misuse or inappropriate use (such as overloading of the device or use of non-approved tools or accessories), failure to comply with the maintenance and safety regulations, ingress of foreign bodies into the device (e.g. sand, stones or dust), effects of force or external influences (e.g. damage caused by the device being dropped) and normal wear resulting from proper operation of the device. The guarantee is rendered null and void if any attempt is made to tamper with the device.
- The guarantee is valid for a period of 3 years starting from the purchase date of the device. Guarantee claims should be submitted before the end of the guarantee period within two weeks of the defect being noticed. No guarantee claims will be accepted after the end of the guarantee period. The original guarantee period remains applicable to the device even if repairs are carried out or parts are replaced. In such cases, the work performed or parts fitted will not result in an extension of the guarantee period, and no new guarantee will become active for the work performed or parts fitted. This also applies when an on-site service is used.
- In order to assert your guarantee claim, please contact the service partner shown below. If the complaint is within the guarantee period, we will provide you with a return slip, with which you can return your defective device free of charge to us. It would help us if you could describe the nature of the problem in as much detail as possible. If the defect is covered by our guarantee then your device will either be repaired immediately and returned to you, or we will send you a new device. Of course, we are also happy offer a chargeable repair service for any defects which are not covered by the scope of this guarantee or for units which are no longer covered. To take advantage of this service, please send the device to our service address.
Service-Hotline (GB):
+800 4003 4003
(0,00 EUR/Min.)
Service-Email (GB):
[email protected]
Service Address (GB):
Forest Park & Garden
Coed Court, Taffsmead Road
Treforest, Ind. Estate, Pontypridd CF375SW
At www.lidl-service.com you can download this and many more manuals, product videos plus installation software.
The QR code takes you directly to the Lidl service page (www.lidl-service.com) and you can open your operating manual by entering the article number (IAN) 361816 _ 2010.
SCHEPPACH FABRIKATION VON HOLZBEARBEITUNGSMASCHINEN GMBH
Günzburger Str. 69
D-89335 Ichenhausen
Last Information Update