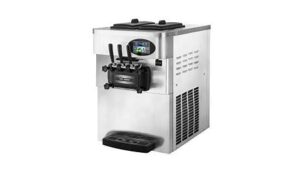
ICE CREAM MACHINE
MANUAL
Structure
Conditions
Our ice cream machine can work under the below conditions:
Ambient temperature: 5~40°C mixture temperature: 2~35°C Power: 110V/60Hz
* The above conditions can directly affect the machine’s performance and capacity.
Installation and Cautions:
Please strictly follow the instruction on the yellow sticker.
- Do not directly connect the machine to the electricity generator.
- Do not directly connect the machine to the battery.
- Put the machine still for 24 hours after transportation before using it.
- Power wire should not exceed 10m.
- The hopper must have a mixture when used.
- The ice cream mixture should be in accordance with the appropriate formula.
- Always use the machine in stable voltage.
- In the case of wire breaking, please hire a technician to fix or replace it.
- DO NOT put any explosive substance in the machines.
- this machine is similar to a home electrical appliance and can be used in the kitchen of shops, offices, farms, motels, hotels, or restaurants catering events to provide instant soft serve ice cream.
3.1 Placement
a. Place the machine on even plain ground.
b. Make sure the machine is in good ventilation, and avoid heat sources or sunlight. Air outlets of the machine should be at least 1m away from walls or any other barriers, other sides should be at least 0.3m away from any barrier.
c. Avoid dust.
3.2 Wiring
a. Make sure the socket is connected to the ground
b. Make sure the power supply has a circuit-breaker or any other device for protection against electric shock.
c. The section area of power code copper core(a) MUST BE 18l machine, 25l machine: a≥2.5mm²—–36l machine: a≥4mm²
d. Under-size power code can result in low voltage and overload, which affect machine performance or cause damage.
3.3 Installation
a. Please check the package and inform the forwarder or our company if any damage, our company will not take any responsibility if the bill is signed.
b. Open the carton box, you will find a parts box in the hopper. In the parts box, you will find handles and consumable parts, keep the spare parts for future replacement.
c. Please check the nameplate on the right panel, and confirm this is the correct model(voltage, frequency, and power) you order.
d. Install the discharger properly, tighten it to the machine with 2 bolts, screw the 2 bolts in diagonal at the same time, make sure no gap between the discharger and the machine, otherwise, water or mixture can leak from it during washing or making ice cream.
e. Install the handles to the valve stems, in the meantime, slowly push the steel pin through the discharger and the handles. (Refer to the below photo for the correct direction of the handles)
f. Install the drain holder to the 2 nuts on the machine, to catch the dripping. DO NOT put heavy object like buckets or basins on them, as it is not designed for holding heavy objects.
How to Make Ice Cream
4.1 Wash
Connect it to a 16A socket, and switch on the power with the stick on the left down part of the control panel. Pour water from the hoppers to fulfill the cylinders, press “WASH”, allow it to run for 2 minutes, then press the handle to directly drain the water in the “WASH” mode. repeat this 2-3 times, until the water that comes out is all clean.
4.2 Make mixture
Currently, in the market, there is a ready-made mixture of ice cream or powder that needs to mix with water. Please follow the instructions and formula on the powder package(generally speaking: 1kg powder to 2.5-3kg water), stir them even, let them completely dissolve and mix together, avoid lumps forming, and leave it still for 30 minutes. These are very important factors for the texture and amount of the ice cream later produced.
4.3 Make ice cream
a. Make sure water is completely drained, then pour the mixture into the hopper.
b. Press “Wash” (beater will start to rotate, to beat it even), after 2 minutes, press “STOP”, then press “Freeze” to start freezing (Notice: Make sure the mixture level in the cylinder should be lower than the inlet of discharger or else can result in loud noise or damage. when you hear scratch sounds between the beater and the cylinder, that means the mixture inside is not enough.)
c. In “Freeze” mode, the screen will show the progress of ice cream making, generally speaking, when it reaches 80%, the ice cream is ready for dispensing. When it reaches 100%, the machine will stop automatically and back to “Standby” mode.
How to Operate
For different stickers on the display, “SOFT & HARD” sometimes are shown as “+ & -”.
a. Standby Mode
The machine is in this mode after switching on when no button is pressed.
b. Wash Mode
Press“WASH”, “WASH” sign will be on, so do the motor, the beaters start to rotate, but the compressor is off.
The machine is now in Wash Mode. To stop and shift back to Standby Mode, press “STOP”.
c. Freeze Mode
Press “FREEZE”, the “FREEZE” sign is on, the motor start to work immediately, after 5 seconds, the compressor will be on,(or else it will start after the return valve shuts.)As the freezing proceeds, ice cream hardness will reach a certain set value, the screen will show 100%, then the compressor will stop, after 15 seconds, the motor stops too, now a complete ice cream making procedure is over. After a certain set length of time (interval time can be adjusted from 5-to 30 minutes, please refer to the table on the latter page), the system will automatically repeat the above-mentioned procedure, Or if the dispensing sensor is triggered, the “FREEZE” Mode will also start all over again. Press “STOP” to turn back to “Standby” mode.
Cylinder chilling is controlled by timing. Users can set a time interval (30-120 minutes) between the chilling processes. The chilling process runs for 10 minutes at most each time, it will also stop if the ice cream hardness inside has reached a set value, and will then starts the countdown for the next cycle.
Maintenance
6.1. Wash Cylinder
Please wash the cylinder once a day to improve the service life of the machine and also to ensure food safety for customers.
a. Press “WASH”, to beat out all the mixture from the cylinder, then press “STOP” (you can also unload the discharger and take out the beater, so to remove the ice cream that sticks on the beater.)
b. (if you take out the beater and discharger, make sure you install them back properly before pouring water in it) Dissolve the proper amount of disinfectant in warm water, and pour it inside the hopper.
c. Press “WASH” to beat for 5 minutes, then drain it.
d. Pour in clear water, to wash 3-5 times, then stop the machine.
e. Turn off the machine, and disassemble all other components (take out valves and O rings from the discharger, and the big silicone O ring from the discharger)
* Please disassemble and wash the components according to the following steps if the machine has stopped serving for a long time.
a. Unscrew all 2 bolts from the discharger, unload the discharger, then disassemble all components from the discharger
b. Take off the pin, handles, valve stems, and silicone O-ring
c. Take the beater, disassemble the silicone seal from the beater end
d. Wash the components thoroughly and replace the broken ones. e. Assemble back all the components. (apply some lubricant to the valve stem for easier assembling the O
rings and the valve stem back to the discharger )
6.2 Wash the screen
Please use a wet cloth to wipe the screen only, avoid pouring water directly on the control board or the inside, or else can result in malfunction.
Error and Solution
When errors occur, the system will shut down all outputs and display an error code, meanwhile, the alarm will keep beeping. Please refer to the below table for code information.
code | problem | cause | solution | remark |
01 | Voltage too low | voltage too low | install a voltage stabilizer. | |
02 | Voltage too high | voltage too high | install a voltage stabilizer. | |
03 | Speed sensor abnormal |
|
|
|
05 | Weak refrigeration | refrigeration system error | Check the system | Some models don’t have a temperature checking function |
06 | Cylinder frozen |
|
|
Some model is without a temperature checking function. |
07 | Cylinder temperature too high. |
|
|
|
10 | Running overtime |
|
|
|
11 | High-pressure protection | Compressor pressure too high | Check refrigeration system | |
Screen problem | No display while machine turned on. |
|
|
Must be performed by a technician. |
4. Check PCB | ||||
Display not clearly |
|
|
Parameters
CODE | INDICATION | REMARK |
P00 | the time interval of auto freeze restarting | Interval can be set between 5-and 30 minutes. |
P01 | Precool temperature | Range from 0-10 ℃, if no precooling function, this code will not show |
P02 | Fresh function in-cylinder interval | Range from 30 to 120 minutes, If no precooling function, this code will not show. |
P03 | reset cone record | Long press “+” or “-” to reset the cone record |
THE BELOW ARE MERELY FOR THE MANUFACTURER’S SETTING | ||
F00 | set over time value | The range is between 30-60 minutes |
F01 | The factor of hardness correction | Range from 1-16, the higher the harder. Factory default is 1. An appropriate setting can result in belt slipping or no auto stop. |
F02 | Value of low voltage protection | Range:110V—120V |
F04 | Rotation speed detection | 1 screen will show the speed if detected, if not, it shows “—”, to delete the existing value, long press “+”or “-” for 5 seconds until it shows “—” If motor or any other speed-relevant components are replaced, please run a speed detection: enter F04 menu, delete the existing value, then run wash mode for 10 seconds, and the detection will be automatically completed. Notice:Please run the rotation speed detection in WASH mode,DO NOT run it with ice cream mixture or water inside the cylinder. |
8.1 How to set parameters
The parameter can be divided into factory parameters (marked “F”) and user parameters (marked “P”).
a. For the user parameter, long-press the “+” or “-” to enter the setting window. In the setting window, press “SET” to shift between different groups of user parameters, and press “+” & “-” to change the value.
b. For factory parameters, long-press both the “SET”& “STOP” at the same time to enter. When getting into the setting window, press “SET” to shift between different groups of parameters. The first several groups are still user parameters, after the last user parameter, you will see the factory parameter. The setting is the same as the user parameters.
Hardness setting
In “Standby”, “Wash” or “Freeze” mode, You can change the hardness set value. Simply long-press the “+”or “-” until the hardness value blinks, then release the button, and click “+” or “-” to adjust the value.
Repair
- Please disconnect power before installing or wiring, always follow the circuit diagram and make sure the power supply is in accordance with that on the nameplate.
- Please hire a professional electrical technician for wiring.
- Make sure all terminals are firmly connected to connectors.
- Keep hands, fluid, or any foreign objects off the PCB, and at least 6mm away from the panels, or else may result in short-circuit and fire.
- In the case of a fuse blew, please check and remove the faults first, then replace it with one of the same specifications
- In the case of replacing the speed sensor, please make sure the parameter which is DC12V NPN, Hall Proximity Switch sensor.
- After replacing a motor or any speed-relevant components, please run a rotation speed detection.
The above-mentioned are common malfunctions. If a more complex problem occurs, please hire a professional technician.