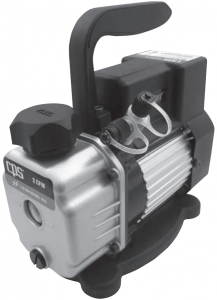
Pro-Set® VACUUM PUMP SERIES
VP & VPC SINGLE – DUAL STAGE VACUUM PUMPS
OPERATION MANUAL
GENERAL INFORMATION
Introduction
Thank you for purchasing the CPS® Pro-Set® VP vacuum pump series. Our vacuum pumps are specifically designed for the air-conditioning and refrigeration service industry. The VP and VPC series both utilize an electrical motor and oil filled rotary vacuum pump cartridge construction.
Features:
- Equipped with our exclusive oil mist free exhaust port
- VP series dual stage models are equipped with gas ballast valve
- The dual voltage models can be quickly converted to 115 or 230 volt operation
- Sure-Grip handle, ergonomically designed for superior comfort and portability
- Solid rubber base provides extreme shock resistance
- Air cooled motor design allows for operation under high temperature conditions
- The VP & VPC series excel in vacuum performance, rated 10-15 microns (Dual Stage) and 50-100 microns (Single Stage)
- All vacuum pumps allow for multiple connections, therefore giving full operational preference
- Accessible oil drain port & sight glass make both oil maintenance and accuracy easy
To help you get a good start, please continue to carefully read the balance of this manual. This manual contains important information on the proper procedures for operating this equipment. Please pay close attention to the: Safety Information, Warnings, and Cautions provided throughout this manual.
ALWAYS REMEMBER ” SAFETY FIRST ”
2
General Safety Instructions
ONLY QUALIFIED SERVICE PERSONNEL SHOULD OPERATE THIS UNIT. SOME COUNTRIES MAY REQUIRE THE USER TO BE LICENSED. PLEASE CHECK WITH YOUR LOCAL
GOVERNMENT AGENCY.
DANGER – Avoid breathing refrigerant vapors and lubricant vapor or mist. Breathing high concentration levels may cause heart arrhythmia, loss of consciousness, or even cause suffocation.
DANGER – ELECTRICAL SHOCK HAZARD – Always disconnect power source when servicing this equipment.
WARNING – Do not operate the vacuum pump on systems under pressure. Damage to the pump may occur.
CAUTION – All hoses may contain liquid refrigerant under pressure. Contact with refrigerant may cause frostbite or other related injuries. Wear proper personal protective equipment such as safety goggles and gloves. When disconnecting any hose, please use extreme caution.
CAUTION – Avoid breathing refrigerant vapors and/lubricant mist. Exposure may irritate eyes, nose, throat and skin. Please read the manufacturers Material Safety Data Sheet for further safety information on refrigerants and lubricants.
CAUTION – To reduce the risk of fire, avoid the use of extension cords thinner than NO. 14 awg. (2,5mm2) to prevent the overheating of this cord please keep length to a minimum.
CAUTION – Do not use this equipment in the vicinity of spilled or open containers of gasoline or other flammable substances. Make certain that all safety devices are functioning property before operating the equipment.
CAUTION: THIS EQUIPMENT IS INTENDED FOR USE OF FINAL EVACUATION OF A REFRIGERANT SYSTEM. THE EVACUATION OF MATERIALS ABOVE 5 PSIG MAY CONTAMINATE OR DAMAGE THE VACUUM PUMP.
CAUTION: DO NOT RUN THIS EQUIPMENT WITH LOW OR NO OIL. RUNNING THIS EQUIPMENT WITH NO LUBRICATION WILL CAUSE PREMATURE FAILURE.
3
GENERAL INFORMATION
Specifications | |||||
* “Blank” = Dual voltage (110-120 / 220 50/60Hz E = 220-240V 50/60Hz J = 100V 50/60Hz U = 115V 50/60Hz | |||||
Model Number | VPC2S* | VPC4S* | VP2S* | VP4S* | VP6S* |
Stages | 1 | 1 | |||
Motor Size (HP) RPM @ 50/60Hz | 1/5
2880 / 3440 |
1/4
2880 / 3440 |
1/4
1440 / 1720 |
1/3
2880 / 3440 |
1/2
2880 / 3440 |
Dimensions (Inches) | 9.1 x 4.5 x 8.0 | 11.3 x 4.5 x 8.0 | 12.2 x 5 x 9.6 | 13.1 x 5.5 x 10 | |
Weight | 9.3 lb / 4.2 kg | 11.0 lb / 5 kg | 13.7 lb / 6.2 kg | 15.0 lb / 6.8 kg | 18.3 lb / 8.3 kg |
Operating Temperature Range | 0˚C (32˚F) to 52˚C (125˚F) | ||||
Power Source Available* | U, E, J | Dual | |||
Ultimate Vacuum | as low as 100 Microns | 50 Microns | |||
Oil Capacity | 9 oz / 250 ml | 10 oz / 300 ml | 16 oz / 470 ml | 16 oz / 470 ml | 19 oz / 550 ml |
Construction | Heavy Gauge Aluminum Chasis with hard rubber base and rubber lined steel handle | ||||
Overload Protection | Motor Thermally Protected, Dual Voltage units have extra IEC fuse | ||||
Control System | ON-OFF power switch | ||||
Free Air Displacement | 2 CFM @ 60Hz
48 l/m @ 50Hz |
4 CFM @ 60Hz
96 l/m @ 50Hz |
2 CFM @ 60Hz
48 l/m @ 50Hz |
4 CFM @ 60Hz
96 l/m @ 50Hz |
6 CFM @ 60Hz
144 l/m @ 50Hz |
Intake Fittings | 1/4 SAE and 1/2 ACME | 1/4 SAE, 3/8 SAE, and 1/2 ACME | |||
Gas Ballast Valve | No |
4
GENERAL INFORMATION
Specifications | |||||||
* “Blank” = Dual voltage (110-120 / 220 50/60Hz E = 220-240V 50/60Hz J = 100V 50/60Hz U = 115V 50/60Hz | |||||||
Model Number | VPC2D* | VP2D* | VP4D* | VP6D* | VP8D* | VP10D* | VP12D* |
Stages | 2 | ||||||
Motor Size (HP) RPM @ 50/60Hz | 1/4
2880 / 3440 |
1/3
1440 / 1720 |
1/2
2880 / 3440 |
1/2
2880 / 3440 |
2/3
2880 / 3440 |
3/4
2880 / 3440 |
1
2880 / 3440 |
Dimensions (Inches) | 11.3 x 4.5 x 8.0 | 12.2 x 5 x 9.6 | 13.1 x 5.5 x 10 | 14.9 x 5.7 x 10.6 | |||
Weight | 12.1 lb / 5.5 kg | 17.7 lb / 8.0 kg | 22.1 lb / 10.0 kg | 22.5 lb / 10.2kg | 29.8 lb / 13.5kg | 30.3 lb / 13.7kg | 30.9 lb / 14.0kg |
Operating Temperature Range | 0˚C (32˚F) to 52˚C (125˚F) | ||||||
Power Source Available* | E, U, J | Dual, E, J | Dual, J | ||||
Ultimate Vacuum | 15 Microns | 10 Microns | |||||
Oil Capacity | 9 oz / 250ml | 11.5 oz / 330ml | 15.5 oz / 450ml | 14 oz / 400 ml | 29 oz/ 860 ml | 28 oz / 830 ml | 27 oz / 800 ml |
Construction | Heavy Gauge Aluminum Chasis with hard rubber base and rubber lined steel handle | ||||||
Overload Protection | Motor Thermally Protected, Dual Voltage units have extra IEC fuse | ||||||
Control System | ON-OFF power switch | ||||||
Free Air Displacement | 2 CFM @ 60Hz 48 l/m @ 50Hz | 2 CFM @ 60Hz 48 l/m @ 50Hz | 4 CFM @ 60Hz 96 l/m @ 50Hz | 6 CFM @ 60Hz 144 l/m @ 50Hz | 8 CFM @ 60Hz 192 l/m @ 50Hz | 10 CFM @ 60Hz 240 l/m @ 50Hz | 12 CFM @ 60Hz 288 l/m @ 50Hz |
Intake Fittings | 1/4 SAE & 1/2 ACME | 1/4 SAE, 3/8 SAE, and 1/2 ACME | 1/4, 3/8 and 1/2 SAE | ||||
Gas Ballast Valve | No | Yes |
5
OPERATION
VP Series Parts
Unit consists of:
- Pro-Set ® model vacuum pump
- CPS® vacuum pump oil
- Operational manual.
6
VPC Series Parts
Unit consists of:
- Pro-Set ® model vacuum pump
- CPS® vacuum pump oil
- Operational manual.
7
Initial Preparation
- If the vacuum pump is equipped with a dual voltage motor, make sure the voltage selector switch is set for the desired voltage operation.
- The vacuum pump is shipped without oil in the reservoir. Remove the exhaust/oil fill cap and add oil until it is seen in the middle of the oil sight glass. Re-secure cap.
- Remove the 1/4″ inlet service port cap, turn on the vacuum pump. After 15 seconds, replace 1/4 cap back on inlet port.
- Re-check vacuum pump oil level. Add or remove oil if necessary.
To achieve good final vacuum levels, the oil level should be visually seen through sight glass.
CAUTION: DO NOT RUN THIS EQUIPMENT WITH LOW OR NO OIL. RUNNING THIS EQUIPMENT WITH NO LUBRICATION WILL CAUSE PREMATURE FAILURE.
VACUUM PUMP IS NOW READY FOR USE.
Vacuum Pump Operation
WARNING: Do not operate on systems under pressure.
- Check the correct power supply outlet to be used.
- The VP series is equipped with a dual voltage motor. Make sure the voltage selector switch is set for the desired voltage operation.
Caution: The motor will overheat and trip the thermal protector if the voltage selector and the power supply voltage do not match. - Connect the correct power cord from vacuum pump to power supply outlet.
- Check oil level in vacuum pump.
- Connect vacuum pump as shown in Figure – 1.
- Open manifold valves.
- Turn vacuum pump power switch “ON”.
- Run vacuum pump until final vacuum level is met.
- Once the final vacuum level is reached, close manifold valves, turn power switch “OFF”.
VACUUM OPERATION COMPLETE
Routine Maintenance
It is recommended to change the vacuum pump oil after 50 hours of usage. The purity of the oil will determine the final vacuum level achieved. Always use the CPS recommended vacuum pump oil (VPOQ / VPOP / VPOG). The oil provided with the pump has been specially blended to maintain maximum visosity at normal running temperatures as well as cold weather starts.
OIL CHANGE PROCEDURES:
- Be sure the pump oil is warmed up. if not warm, turn vacuum pump “ON” for 10 minutes.
- Make sure vacuum pump is not plugged in.
- Remove the oil drain cap and drain the contaminated oil into a suitable container. Tilt the vacuum pump toward the oil drain port.
- Once all the oil has been drained, re-secure the oil drain cap back onto the oil drain port.
- Remove the exhaust / oil fill cap and add oil until it is seen in the middle of the oil sight glass. Re-secure exhaust/oil fill cap.
9
Troubleshooting Chart
Condition | Possible Problem | Solution |
Unusually noisy | 1. Bad bearings.
2. Loose motor bolts. 3. Coupling drive. 4. Dirty, low, or improper oil. 5. Air leaks in connections. |
1. Replace motor.
2. Tighten bolts. 3. Adjust or replace coupling. 4. Replace oil. 5. Fix leaks. |
High temperature | 1. Low or improper voltage.
2. Worn bearings. 3. Low oil level. |
1. Check power source voltage.
2. Replace motor. 3. Add or replace. |
Poor vacuum | 1. System leaks.
2. Low oil level. 3. Dirty oil. 4. Air leaks at connection. 5. Air leak through seal. 6. Worn rotary mechanism. |
1. Fix leaks.
2. Add or replace oil. 3. Flush and replace oil. 4. Fix leaks. 5. Replace shaft seal. 6. Replace cartridge. |
Oil leaks | 1. Oil leaks through exhaust.
2. Oil leaks through shaft seal. 3. Oil leaks through reservoir. 4. System vented pressure. 5. Pump tipped over. |
1. Oil level too high.
2. Replace shaft seal. 3. Tighten bolts or replace gasket. 4. Check oil level. 5. Check oil level. |
Pump does not start | 1. No power to motor.
2. Damaged motor. 3. Thermal cutout. |
1. Check fuses in IEC panel.
2. Replace motor. 3. Wait for thermal switch to reset. Check for cause of thermal. |
Thermal cutout | 1. Low or incorrect voltage.
2. Cold weather. 3. Dirty Oil. |
1. Check voltage, move voltage selector switch to correct setting.
2. Start and run vacuum pump with the intake fitting open for 1 minute to warm up oil. 3. Flush and replace oil. |
10
Learn more about automotive A/C tools and equipment we have.